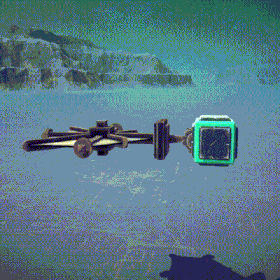
Return-to-Center (RTC) refers to multiple technologies for powered joints, which all do the same thing:
- When its key is pressed, the hinge rotates outward to a limited angle.
- When its key is released, the hinge rotates back to its original position.
RTC joints have several important uses, mostly around machine attitude control:
- Aircraft control surfaces
- Car/truck steering
- Thrust vectoring
With the advent of Automation and RTC Steering Hinges, RTC can also be used for single-press toggleable rotation, e.g.:
- Retractable landing gear
- Aircraft flaps
- Missile/bomb bays
Steering Hinge[]
RTC technologies came about in the first place because steering hinges originally didn't have angle limits or return-to-center functionality.
Now, they do.
Advantages[]
- Super-simple design (it's one block)
- Easy construction and configuration
Disadvantages[]
- Return speed is half of the set hinge speed, capped at 1.2x (at 2x speed)
- Can be floppy, depending on implementation
It might be noted that slower return speed is not necessarily a problem, outside of low timescales or tight timing requirements. This problem can also be remedied by combining it with Toring.
Floppy hinges can be cured by scaling them flat and wide, thanks to how Rigidity works, but this can make them tricky to fit.
Examples[]
Toring[]
Toring (or torque imperfection steering) centers around twisting a static joint with a motor (e.g. Powered Wheel). Even in the era of RTC steering hinges, they carve out a niche with fast return speed and high rigidity-to-size ratio.
- The stator is the base block of the joint, which is static. Higher mass (0.5x-1x) increases angle limit (particularly at high rotor speed), but also increases risk of things breaking.
- The rotor is the motor which rotates the joint. Higher speed increases angle limit.
- The torsion bar is the joint which the rotor is twisting, and is connected to the rotor and stator. Lower scale (0.2x) increases both travel time and angle limits. At low scales, mass also affects both travel time and angle limits.
Types[]
- Cog: Uses an Unpowered Cog with 'frozen' turned on as the torsion bar.
- Inline - The torsion bar and rotor are placed either side of a block and fixed in place. The 'stator' moves.
- Offset - Can be constructed without scaling using a Powered Cog rotor moved 0.5m forward/backward.
- Basic - Can be constructed in basic vanilla by using the unpowered cog to physically resist the powered cog.
- Grabber: Uses a Grabber as the torsion bar.
- Steering Block: Uses a Steering Block as the torsion bar.
- Variable Mass: Uses only a Scaling Block/Ballast as the torsion bar.
- Brace + Variable Mass: Uses a low-mass Scaling Block/Ballast as the torsion bar, but Braces it to the stator.
The torsion bar doesn't necessarily need to be connected directly to the rotor; it can be braced.
Advantages[]
- Strong and fast
- Easy to tune angle limits (to a degree)
- Return speed is same as or faster than outward speed
Disadvantages[]
- Difficult and unintuitive to build
- The nature of secondary connections might make connecting things to the joint difficult
- Using the same block as the stator for two identical toring setups will result in the setups acting differently. DO NOT DO THIS.
Examples[]
Pistons[]
Piston RTC converts the linear motion of Pistons into rotation by pushing a secondary joint attached to the primary joint.
It was the first RTC technology to be created, and was widespread even after toring was developed due to being easier to understand and build. However, with the advent of steering hinge RTC it quickly disappeared.
- The primary joint is where the RTC rotation happens.
- The secondary joint is another joint attached to the primary joint, where the linear motion of the piston is converted to rotate the primary joint.
Types[]
- Common RTC (CRTC): Two pistons are placed either side of a block and braced together; the pistons are then connected to the secondary joints. The pistons move outward/inward.
- Piston Stack: Similar to CRTC, except two pistons are stacked; the outer piston is braced to the inner block, and the inner piston is braced to the secondary joint. This is more compact (and ideal for aircraft), but often has asymmetric rotation.
- Big Black RTC (BBRTC): Two secondary joints and attached pistons are connected either side of the primary joint pushing forward/backward. The pistons are static.
- When Scaling is involved, this method is more compact, symmetrical, and powerful than piston stacks for control surfaces.
- For cars, it is necessary to connect the assembly to a block, which is then connected to more secondary joints.
Advantages[]
- Easier to build than toring
- Return speed is same as outward speed
Disadvantages[]
- Bulky and complex
- Difficult to tune angle limits or torque
- Weak
Examples[]
Others[]
- Other attitude control systems which have RTC-like behaviour but which aren't strictly RTC joints are Reaction Wheels and thruster control with Flying Blocks or Water Cannons.
- Before piston RTC, many players tried using Contractible Springs for RTC joints. They found quickly that this was not viable because springs short enough to fit on an aircraft have no pulling power whatsoever.