铣刀
此条目翻译品质不佳。 (2019年6月27日) |
铣刀是通常用于铣床或加工机的切削工具,以执行铣削操作(有时在其他机床中)。它们通过其在机器内固定的进给率进行移除材料。
铣刀的特点
[编辑]
铣刀具有几种形状和许多尺寸。 还可以选择涂层,以及螺旋角和切割面数量。
- 形状:铣刀的几种标准形状在当今的工业中被使用,这在下面将更详细地解释。
- 排屑槽 / 刀刃:铣头的凹槽是沿著切割器运行的深螺旋槽,而沿著凹槽边缘的锋利刀片被称为刃。刃切割材料,并且该材料的切屑通过旋转中的钻头推出排屑槽。每个排屑槽几乎总是有一个刀刃,但是一些切割器每个排屑槽有两个刀刃。[1] 通常,排屑槽和刀刃可以互换使用。 铣刀可能有一个到多个刀刃,2刃、3刃和4刃是最常见的。通常,刀刃具有的齿越多,其能够更快地去除材料。因此,4齿刀可以比2齿切削刀的两倍速度去除材料。
- 螺旋角:铣刀的槽纹几乎总是螺旋形的。如果排屑槽是直的,整个刀刃会立即冲击材料,造成振动,降低精度和表面质量。以一定角度设置排屑槽可以使刀刃逐渐进入材料,减少振动。通常,精加工刀具具有更高的螺旋角以得到更好的加工。
- 中心切割:有一些铣刀可以通过材料直线向下钻,大部分铣刀是不能直线向下。这是因为刀具的刀刃不能一直到达终端的中心。但是,这些刀具可以以45度左右的角度向下切割。
- 粗加工或整理:不同类型的铣刀可用于切割大量材料,留下不良的表面光滑度(粗加工),或去除较少量的材料,但留下良好的表面光滑度(精加工)。粗加工刀具可以具有用于将材料碎屑破碎成更小片的锯齿状齿。这些刀刃留下了粗糙的表面。精加工刀具可以具有大量(4个或更多个)刀刃,用于小心地去除材料。然而,大量的槽纹几乎没有有效的切屑去除的馀地,因此它们不太适合去除大量的材料。
- 涂层:正确的工具涂层可以通过提高切割速度和刀具寿命以及改善表面光洁度对切割过程产生很大的影响。合成钻石(PCD)是用于刀具的特殊硬涂层,必须承受高磨损。PCD涂层的工具可以比未涂覆的工具长达100倍。然而,涂层不能在高于600摄氏度的温度或黑色金属上使用。铝加工的工具有时会被涂覆氮化铝钛。铝是一种相对较粘的金属,可以将其自身焊接到工具的牙齿上,使它们看起来钝。然而,它倾向于不粘附TiAlN,允许该工具在铝中使用更长时间。
- 柄:柄是刀具的圆柱形(非凹槽)部分,用于将其固定并定位在刀架中。柄可以是完全圆形的,并且通过摩擦保持,或者可以具有焊接平面,其中定位螺丝也称为无头螺丝在没有工具滑动的情况下接触以增加扭矩。直径可能与工具的切割部分的直径不同,因此可以由标准的工具夹保持。
选择铣刀
[编辑]选择铣刀不是一件简单的工作。有很多变数,意见和理由需要考虑,但基本上师傅正在努力选择一种能够以最低成本将材料切割成所需规格的工具。工作的成本少部分来自于工具的价格,铣床所花费的时间以及师傅花费的时间的组合。通常,对于大量零件的工作和加工时间的日子,工具的成本是三个成本中最低的。
- 材料:高速钢(HSS)铣刀是最便宜和寿命最短的铣刀。与常规高速钢相比,含钴高速钢通常可以运行10%更快。硬质合金工具比钢更昂贵,但持续时间更长可以运行得更快,从长远来看证明更经济。[来源请求] HSS工具完全适用于很多应用。从常规HSS到钴HSS到碳化物的发展可以被认为是非常好的。使用高速主轴可能会排除HSS的使用。
- 直径:较大的工具可以比较小的工具更快地去除材料,因此通常会选择适合工作的最大可能的刀具。当铣削内部轮廓或凹入的外部轮廓时,直径受内部曲线的大小限制。刀具的半径必须小于或等于最小弧的半径。
- 排屑槽:更多的槽纹允许更高的进给速率,因为每个排屑槽有较少的材料被去除。但由于核心直径增加,切屑的空间较小,因此必须选择平衡。
- 涂料:诸如氮化钛等涂料也增加了初始成本,但减少了磨损并延长了刀具寿命。TiAlN涂层减少铝对工具的粘附,减少并有时消除了润滑的需要。
- 螺旋角:高螺旋角通常是软金属最好的,硬质或韧性金属的螺旋角较低。
类型
[编辑]端铣刀
[编辑]
立铣刀(图中的中间排)是在一端以及侧面具有切削齿的那些刀具。立铣刀一词通常用来指平底刀,而且还包括圆形刀具(称为“球头”)和圆角铣刀(简称“大鼻子”)或“ 'torus')。 它们通常由高速钢或硬质合金制成,并具有一个或多个凹槽。它们是立式磨机中最常用的工具。
粗加工立铣刀
[编辑]粗加工立铣刀快速清除大量物料。这种立铣刀使用在周边切割的波浪形齿形。这些波浪形齿形成许多连续的切削刃,产生许多小的切屑,导致相对粗糙的表面光洁度。在切割过程中,多个齿与工件接触减少颤动和振动。用铣削切削快速切削刀片有时被称为铣削。
面铣刀
[编辑]
面铣刀,它们的形状像一条管(但具有较厚的壁),其本体的周围及侧面具有刀刃。
使用铣刀
[编辑]碎片形成
[编辑]尽管有多种不同类型的铣刀,但是了解切屑的形成对于使用它们是至关重要的。当铣刀旋转时,待切割的材料被送入其中,并且切割器的每个齿切掉一小块材料。实现正确的碎片尺寸至关重要。该碎片的尺寸取决于几个变量。
- 表面切割速度 (Vc)
- 这是刀具旋转时每根牙齿穿过材料的速度。这是以公制国家/分钟的米/秒或美国每分钟表面英尺(SFM)来衡量的。某些钢的切割速度的典型值为10m/min至60m/min,铝为100m/min和600m/min。这不应该与进给速率混淆。该值也称为“切向速度”。
- 主轴转速(S)
- 这是刀具的转速,以每分钟转数(rpm)测量。 典型值为数百 rpm,高达数万 rpm。
- 刀具直径(D)
- 齿数(z)
- 每齿进给(Fz)
- 这是当每个齿旋转时材料被送入刀具的距离。 这个值是牙齿最深切割的大小。
- 进料速率(F)
- 这是材料进给刀具的速度。典型值为 20mm/min 〜 5000mm/min。
- 切削深度
- 这是工具在待切割材料表面下的深度。这将是芯片生产的高度。通常,切割深度将小于或等于切割工具的直径。
师傅需要三个值:S, F和深度 在决定如何使用新工具切割新材料时。 但是,他可能会被赋予价值 Vc和 Fz从工具制造商。 S和F可以从他们计算:
主轴转速 | 进料速率 |
---|---|
从主轴速度S的公式来看,可以看出,较大的刀具需要较低的主轴转速,而小型刀具可能会以高速运转。 | 进料速率F的公式表明,增加S或z可以提供更高的进料速率。因此,师傅可以选择具有最高数量的牙齿的工具,该刀具仍然可以应付切屑负荷。 |
逆向铣削与顺向铣削
[编辑]
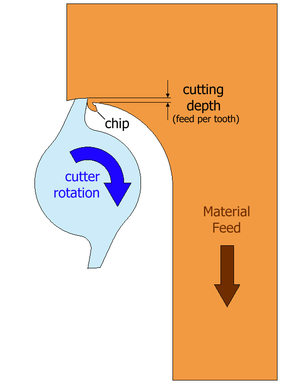
铣刀可以在两个方向做切割,有时称为逆向或上、顺向或下。
- 逆向铣削(左):切削厚度从零厚度开始,并增加到最大值。切割在开始时如此轻巧,刀具不切割,但滑过材料表面,直到足够的压力被建立,牙齿突然咬伤并开始切割。这会使材料变形(图中的点A,左侧)、并使工具变钝在材料上留下不好的表面。
- 顺向铣削(右):每个刀刃在一定的位置接合材料,并且切割的宽度从最大值开始减小到零。芯片设置在切割器后面,导致切屑更容易拆卸。刀刃不会磨擦材料,因此刀具寿命可能会更长。然而,爬升可以对机器施加较大的负载,但是不建议用于较旧的铣床或机器。
刀具位置(刀具半径补偿)
[编辑]刀具位置是为了实现所需工件轮廓(几何形状)而定位刀具的位置,因为刀具尺寸不为零。最常见的示例是刀头半径补偿(CRC),其中刀具的中心线将通过“距离”等于刀具半径的向量偏离目标位置,并且其“方向”为由常规铣削与爬坡 左/右,爬升/常规,上/下区别统治。
在G-code的大多数实现中,控制CRC(G40取消,G41左/爬,G42右/常规)是G40至G42。每个刀具的半径值由CNC操作员或机械师输入到偏移量寄存器中,然后在生产过程中对其进行调整,以使成品尺寸保持在公差范围内。使用球磨机进行3轴,4轴或5轴铣削的3D轮廓的切割器位置由CAM软件轻松处理,而不是手动编程。
通常,通过针对特定CNC控制模型量身定制的后处理器程序将CAM向量输出后处理为G代码。一些后期型CNC控制器直接接受矢量输出,并在内部进行伺服输入的转换。
清除切屑
[编辑]铣刀的另一个重要品质是考虑切削加工产生的切屑的能力。如果切屑没有像产生的那样快速移动,则凹槽会阻塞并有效地防止刀具切割,导致振动,刀具磨损和过热。影响切屑消除的几个因素,包括凹槽的深度和角度,切屑的尺寸和形状,冷却剂的流动以及周围的材料。可能很难预测,但是一个好的机械师会注意切屑堆积,并且如果观察到的话调整铣削条件。
参考文献
[编辑]- ^ Rapid Traverse: More Teeth Per Flute 互联网档案馆的存档,存档日期2007-09-27.
参考书目
[编辑]- De Vries, D., Milling machines and milling practice: a practical manual for the use of manufacturers, engineering students and practical men, London: E. & F.N. Spon, 1910. Coedition, New York, Spon & Chamberlain, 1910.
- Template:Roe1916
- Woodbury, Robert S., History of the Milling Machine. In Studies in the History of Machine Tools, Cambridge, Massachusetts, USA, and London, England: MIT Press, 1972 [1960], ISBN 978-0-262-73033-4, LCCN 72006354. First published alone as a monograph in 1960.