Konstrukcijski čelik



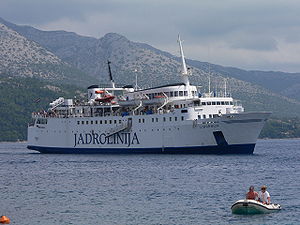




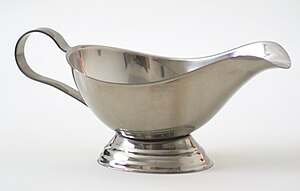
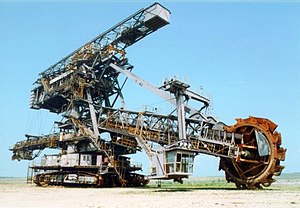


Konstrukcijski čelik je ugljični čelik (obični ili plemeniti) s udjelom ugljika manjem od 0,6% (maseni udio) ili legirani čelik (uglavnom s manganom, silicijem, kromom, niklom, volframom). Koriste se za izradu čeličnih konstrukcija, sastavnih dijelova strojeva, aparata i različitih uređaja. Razlikuju se obični (ugljični ili niskolegirani) čelici za opću masovnu upotrebu i plemeniti (rafinirani) ugljični ili legirani čelici za dijelove s većim zahtjevima (dijelovi strojeva itd.).
Konstrukcijski čelici se koriste kod izrade karakterističnih konstrukcijskih dijelova strojeva i uređaja. Najčešće služe za izradu vratila, osovina, zupčanika, nosača opruga, vijaka, poklopaca, ventila, kućišta itd. S obzirom na mehanička svojstva, konstrukcijski čelici moraju imati visoku granicu razvlačenja, dovoljnu plastičnu deformabilnost (radi izbjegavanja pojave krhkog loma), visoku granicu puzanja i čvrstoću pri povišenim temperaturama, te zadovoljavajuću žilavost i dinamičku izdržljivost. Pored toga, konstrukcijski čelici moraju biti otporni na trošenje i koroziju, te obradivi odvajanjem čestica (rezanje), zavarljivi, skloni hladnom oblikovanju (savijanje, štancanje, duboko vučenje) itd.
Općenito se konstrukcijski čelici mogu podijeliti na ugljične (nelegirani) i legirane. Konstrukcijski čelici (nelegirani i legirani koji sadrže ugljika manje od 0,60%) često se primjenjuju za izradu strojeva i uređaja koji rade u neagresivnim sredinama i pri temperaturama od -25 do 300 °C, kao i za nosive i građevinske konstrukcije.
Ugljični ili nelegirani čelici običnog kvaliteta svrstavaju se pretežno prema mehaničkim svojstvima, te se koriste za slabije opterećene dijelove strojeva, uređaja, vozila ili za šipke i rešetke (npr. čelik S185). Svi nelegirani čelici običnog kvaliteta primjenjuju se u sirovom stanju (bez toplinske obrade). [1]
Opći konstrukcijski čelici obuhvaćaju najširu grupu konstrukcijskih čelika, a najčešće se primjenjuju kod nosivih zavarenih konstrukcija velike mase. Ova skupina čelika najčešće se koristi za izradu mostova, dizalica, nosača, brodskih konstrukcija, dijelova vozila, opreme u industriji nafte i plina i dr. Opći konstrukcijski čelici dijele se na:
- ugljične čelike za nosive konstrukcije i
- čelike za strojogradnju.
Čelici za nosive konstrukcije trebaju ispuniti određene zahtjeve u pogledu nosivosti i sigurnosti. Navedeni zahtjevi mogu se ostvariti ukoliko čelik ima dovoljno visoku granicu razvlačenja, vlačnu i tlačnu čvrstoću, savojnu čvrstoću, smičnu čvrstoću i žilavost. Zavarljivost spada među glavna tehnološka svojstva koje trebaju posjedovati čelici za nosive konstrukcije. Preduvjet za dobru zavarljivost je što niža vrijednost ekvivalenta ugljika (CE):
- CE = %C + %Mn/4 + (%Cr + %Mo + %V)/5 + (%Ni + %Cu)/10
Vrijednost ekvivalenta ugljika prihvatljiva za čelike za nosive konstrukcije iznosi CE < 0,4.
Budući da kod ove skupine čelika kemijski sastav nije zajamčen, te zbog veće prisutnosti nečistoća u odnosu na ostale čelike, opći konstrukcijski čelici nisu predviđeni za toplinsku obradu. Čelici za nosive konstrukcije uglavnom se dijele na osnovi vrijednosti granice razvlačenja i udarne radnje loma. Označavanja konstrukcijskih čelika je uobičajeno prema normi EN 10027-1.
Čelici za nosive konstrukcije posjeduju granicu razvlačenja od 190 do 370 N/mm2, vlačnu čvrstoću od 330 do 700 N/mm2, te istezanje od 10 do 28%. Iznos granice razvlačenja je viši ukoliko je viši sadržaj ugljika i udio perlita u mikrostrukturi. Čvrstoća se može povisiti dodatkom mangana i silicija (mangan mora biti < 1,65% jer povisuje prokaljivost). Porastom omjera Mn/C raste i udarna radnja loma. Čelici za nosive konstrukcije uglavnom se primjenjuju u temperaturnom području od -40 °C do +50 °C. Uobičajeni čelici ove skupine prema EN 10027 su: S235 (Č. 0270), S355J2G3 (Č. 0563).
Čelici za strojogradnju se primjenjuju za strojne dijelove koji se gibaju u odnosu na druge dijelove stroja ili prenose sile i momente. Najčešće se koriste za izradu osovina u kliznim ležajevima, vretena, slabije opterećenih zupčanika, te raznih klinova, vijaka, ručica, poluga i sl. U pogledu zavarljivosti i žilavosti prema čelicima za strojogradnju nema nikakvih zahtjeva. Ova skupina konstrukcijskih čelika slabije je zavarljiva zbog viših udjela ugljika, ali iskazuje višu vlačnu čvrstoću (500 - 700 N/mm2) i nižu istezljivost (10 - 20%) od čelika za nosive konstrukcije. Iako imaju viši sadržaj ugljika nisu namijenjeni za kaljenje. Uobičajeni čelici ove skupine prema EN 10027 su: E295 (Č. 0545) s oko 0,3% C, E335 (Č. 0645) s oko 0,4% C, te E360 (Č. 0745) s oko 0,5% C. [2]
Povećanje čvrstoće čelika, uz istovremenu uštedu legirajućih elemenata, ostvaruje se primjenom postupka mikrolegiranja. Mikrolegiranje se koristi prvenstveno kod izrade konstrukcijskih čelika koje karakterizira visoka granica razvlačenja, zadovoljavajuća plastičnost, neznatna sklonost krhkom lomu, te dobra zavarljivost. Razvoj zavarljivih konstrukcijskih čelika započinje krajem 20-ih godina 20. stoljeća. U početku proizvodnje takvih čelika osnovni cilj bio je povećanje čvrstoće, odnosno granice razvlačenja. Međutim, polazeći od sve naglašenijih potreba za uštedom materijala i energije u posljednje vrijeme sve se veći značaj usmjerava prema žilavosti, zavarljivosti i sposobnosti oblikovanja.
Za sve moderne visokočvrste zavarljive čelike karakteristično je da su mikrolegirani s niobijem, vanadijem, titanijem ili nekim drugim mikrolegirajućim elementom. Razlika u odnosu na uobičajen sastav konstrukcijskih čelika je u relativno niskom sadržaju ugljika i dodatku mikrolegirajućeg elementa. Sadržaj mikrolegirajućeg elementa u mikrolegiranim čelicima iznosi od 0,01 do 0,1%, a sadržaj ugljika je vrlo nizak (0,02 - 0,20%). Mikrolegirajući elementi ne mijenjaju osnovnu vrstu čelika tj. nelegirani čelik ostaje nelegiran, niskolegirani čelik ostaje niskolegiran.
Sitnozrnati čelici su razvijeni prvenstveno iz čelika za nosive konstrukcije, kao što su S355J0G3 (Č. 0562) i S355J2G3 (Č. 0563). Budući da su umireni aluminijem i silicijem, imaju sitniju feritno-perlitnu mikrostrukturu, te zadovoljavajuću zavarljivost. Povišenjem udjela perlita (viši udio ugljika) može se postići visoka čvrstoća, ali tada opada zavarljivost i žilavost. Daljnim razvojem ove skupine čelika dodavani su mangan, nikal i krom kao legirajući elementi radi povišenja čvrstoće mehanizmom očvršćivanja pomoću kristala mješanaca (ferita). Međutim, posljedica takvog načina povišenja čvrstoće su pogoršana tehnološka svojstva (raste sklonost zakaljivanju pri zavarivanju).
Poboljšani sitnozrnati čelici razvijeni su u trećem stadiju razvoja čelika za nosive konstrukcije. Glavna karakteristika ovih čelika je da su kaljeni u vodi s temperature oblikovanja, te dodatno popušteni pri temperaturi 680 - 710 °C. Zahtjevi u pogledu mogućnosti dobrog zavarivanja ove skupine čelika uvjetovali su da svi čelici iz ove skupine konstrukcijskih čelika sadrže ispod 0,2% ugljika. Niskougljični martenzit je najpogodniji za postizanje zadovoljavajuće kombinacije čvrstoće i žilavosti. U odnosu na feritno-perlitnu i bainitnu mikrostrukturu, martenzit je izrazito neosjetljiv na krhki lom.
Osim klasičnih postupaka proizvodnje konstrukcijskih čelika u drugoj polovici 20. stoljeća, razvijena je nova tehnologija koja je obuhvaćala i toplinsku obradu, pa je takav postupak nazvan termomehanička obrada. Takvim načinom proizvedeni čelici već u valjanom stanju, posjeduju povoljnu granicu razvlačenja i otpornost prema krhkom lomu. Međutim, termomehanička obradba je djelotvorna samo ukoliko je sadržaj ugljika vrlo nizak, pa ne utječe na povišenje čvrstoće. Takvi čelici predstavljaju treću skupinu zavarljivih konstrukcijskih čelika povišene čvrstoće, koja se od prve dvije grupe (normalizirani, poboljšani) razlikuje po kemijskom sastavu, načinu proizvodnje i mehanizmu povišenja čvrstoće.
Čelični proizvodi izrađeni od čelika iz ove skupine konstrukcijskih čelika(zajamčen sastav i svojstva) prije primjene podvrgavaju se postupku kaljenja, tj. pretvorbi austenita u ugljični martenzit. Ukoliko se zakaljeni proizvod popušta nisko (<250 °C) njegovo stanje se naziva kaljenim, a ukoliko se popušta visoko (>500 °C) stanje mu se naziva poboljšanim. Učinak kaljenja procjenjuje se pomoću zakaljivosti i prokaljivosti čelika. Zakaljivost predstavlja sposobnost čelika da gašenjem poprimi što višu tvrdoću, a prokaljivost predstavlja sposobnost što jednoličnije tvrdoće.
Čelici za cementaciju predstavljaju konstrukcijske čelike kojima se nakon obrade odvajanjem čestica pougljičava rubni sloj. Nakon pougljičavanja rubnog sloja provodi se kaljenje kako bi se postigla visoka otpornost na trošenje rubnih slojeva, te povišena žilavost nepougljičene jezgre. Čelici za cementaciju uglavnom sadrže 0,1 - 0,2% ugljika prije pougljičavanja, a mogu biti ili nelegirani ili niskolegirani. Nakon pougljičenja rubni sloj sadrži 0,8 - 0,9% ugljika, te se zakaljivanjem postiže tvrdoća 61 - 64 HRC.
Čelici za poboljšavanje pripadaju skupini nelegiranih ili niskolegiranih konstrukcijskih čelika koji kaljenjem i visokim popuštanjem (> 500 °C) postižu odgovarajuću granicu razvlačenja, vlačnu čvrstoću i žilavost. Kaljenjem se nastoji postići što potpunija martenzitna mikrostruktura po presjeku, tj. što viša prokaljenost. Ova skupina čelika sadrži 0,25 - 0,60% ugljika koji utječe na njihovu zakaljivost. U čelike za poboljšanje ubrajaju se i čelici za cementaciju koji nisu pougljičeni, ali su kaljeni s temperature austenitizacije jezgre, te popušteni pri temperaturi oko 200 °C ili iznad 500 °C.
Glavni zahtjev koji se postavlja pred čelike za opruge je da pod djelovanjem radnog opterećenja postignu traženu elastičnu deformaciju. U pogledu elastičnih deformacija svi čelici ostvaruju jednako opružno djelovanje koje je posljedica istog modula elastičnosti i modula smičnosti u slučaju torzijski (uvijanje) opterećenih opruga. Iz toga slijedi da će svaki čelik imati isto opružno djelovanje dok mu je naprezanje niže od granice razvlačenja. Povećanje opterećenja koje opruga može izdržati postiže se proširenjem područja elastičnosti, tj. što višom granicom razvlačenja i granicom elastičnosti. Povišenje granice razvlačenja može se postići povišenjem masenog udjela ugljika, te legiranjem sa silicijem, manganom, kromom i vanadijem.
Čelici poboljšane rezljivosti namijenjeni su za izradu dijelova na visokoproduktivnim automatskim strojevima, pa se često nazivaju i čelicima za automate. Najvažnije svojstvo čelika za automate je bolja obradivost odvajanjem čestica (rezljivost) u odnosu na druge čelike. Bolja rezljivost je karakterizirana sporijim trošenjem oštrice alata, te dobivanjem visoke kvalitete površine. Sposobnost obrade ovi čelici postižu pomoću izmjenjenog kemijskog sastava kojim se pospješuje stvaranje uključaka. Uključci omogućuju stvaranje lomljive i kratke strugotine. Međutim, zbog prisutnosti uključaka ovi čelici su skloniji pojavi krhkog loma, pukotina tijekom toplinske obrade, lomu uslijed zamora i sl.
Nitriranje je jedan od najvažnijih postupaka površinske termokemijske obrade, koji je u komercijalnoj primjeni od 20-ih godina 20. stoljeća. Postupak nitriranja se temelji na difuziji dušika u površinski sloj obrađivanog predmeta. Nitriranje se provodi radi postizanja visoke površinske tvrdoće, poboljšanja otpornosti na trošenje i zamor, bolje korozijske otpornosti s neznatnim promjenama u dimenzijama i svojstvima obrađivanih predmeta.
Dobivena tvrdoća se temelji na promjeni kemijskog sastava površinskog sloja i prisutnosti nitrida, a ne na promjeni mikrostrukture naglim hlađenjem. Postupak se provodi tako da se pripremljeni predmeti (bez oksida, masti i drugih nečistoća) ulažu u peć i izlažu djelovanju sredstva za nitriranje na temperaturi ispod A1 točke, kako ne bi došlo do transformacije ferita u austenit. U pravilu nitriraju se svi čelici, sivi lijev, čelični lijev (u temperaturnom području 500 - 590 °C) i Ti-legure (750 - 900 °C). Plinsko nitriranje se ne preporuča za ugljične čelike, jer se dobiva krhka površina s malim porastom tvrdoće u difuzijskoj zoni. Legirani čelici, zbog izlučivanja nitrida u difuzijskom sloju, pružaju veću otpornost na trošenje i omogućuju primjenu većih površinskih tlakova.
Korozija predstavlja razaranje metala ili legura zbog njihovog djelovanja s vanjskim medijem. Uvjeti međudjelovanja i svojstva medija određuju vrstu korozije pa tako postoji plinska, atmosferska, podvodna, biološka korozija itd. Prema načinu razaranja metala postoje slijedeći oblici korozije: opća (jednolično odnošenje površine), jamičasta (točkasta, rupičasta, “pitting“), interkristalna, napetosna itd. Korozijska postojanost predstavlja sposobnost materijala da se suprotstavi negativnom djelovanju korozijskog medija pomoću usporavanja njegovog djelovanja. [3]
Da bi čelik bio korozijski postojan (pasivan) moraju biti ispunjena dva glavna uvjeta:
- legiranje s barem 12% kroma (moderni nehrđajući čelici sadrže i do 30% kroma),
- postojanje homogene monofazne feritne, austenitne ili martenzitne mikrostrukture, radi izbjegavanja opasnosti od nastanka područja s različitim elektropotencijalom od potencijala osnovne mase.
Prvi austenitni manganski čelik otporan na trošenje koji sadrži oko 1,2% C i 12% Mn (C:Mn=1:10) izumio je Sir Robert Hadfield 1882. Hadfieldov čelik je jedinstven po tome što posjeduje kombinaciju visoke žilavosti i istezanja, s visokim kapacitetom očvršćivanja, te dobrom otpornosti na trošenje. Zbog toga je takav čelik vrlo brzo prihvaćen kao vrlo koristan inženjerski metalni materijal prvenstveno u području građevinarstva (mehanizacija), rudarstva, industrije nafte i plina, u proizvodnji cementa, za izradu dijelova drobilica, mlinova, bagera, pumpi za transport šljunka i kamena, vojnoj industriji itd.
U međuvremenu, predložene su brojne varijacije originalnog manganskog austenitnog čelika, ali samo nekoliko njih je usvojeno kao značajno poboljšanje. Poboljšanje sastava manganskih čelika obično uključuje promjenu sadržaja ugljika i mangana, sa ili bez dodatnih legirajućih elemenata (kao što su npr. krom, nikal, molibden, vanadij, titanij i bizmut).
Prema temperaturnom području primjene čelici namijenjeni za rad pri povišenim temperaturama dijele se na:
- ugljične (čelici za kotlovski lim),
- niskolegirane (najčešće dodaju samo molibden ili kombinacija molibdena i kroma, te kod nekih vrsta i manje količine vanadija),
- visokolegirane martenzitne (sadrže oko 1% molibdena i do 12% kroma) i
- visokolegirane austenitne čelike (austenitni Cr-Ni čelici imaju vrlo visoku temperaturu rekristalizacije (900-1000 °C), pa se mogu dugotrajno primjenjivati pri temperaturama 600 - 750 °C). [4]
Poznato je da sniženjem temperature kojoj je čelik izložen može doći do smanjenja duktilnosti, udarne radnje loma, toplinske istezljivosti i vodljivosti, te specifičnog toplinskog kapaciteta. Pri niskim temperaturama primjene čelika može doći do porasta tvrdoće, vlačne čvrstoće i granice razvlačenja. Najopasniju pojava koja se javlja tijekom izloženosti čelika niskim temperaturama predstavlja sniženje žilavosti.
U primjeni se razlikuju tri osnovne skupine čelika za rad pri niskim temperaturama:
- niskolegirani (mikrolegirani) sitnozrnati čelici, čija je niža prijelazna temperatura žilavosti posljedica sitnog kristalnog zrna, dezoksidacije aluminijem i silicijem, te više čistoće od klasičnih konstrukcijskih čelika,
- čelici za poboljšanje, legirani s 1,5 - 9% nikla, koji pospješuje stvaranje sitnijeg zrna i vrlo žilavog Fe-Ni martenzita nakon kaljenja,
- austenitni čelici Cr-Ni, Cr-Ni-N (Nb, Ti), Cr-Ni-Mo-N i Cr-Mn-Ni-N, koji i blizu apsolutne nule imaju zadovoljavajuću žilavost.
Pored postizanja visoke vlačne čvrstoće i granice razvlačenja, visokočvrsti čelici moraju posjedovati i visoku žilavost, visoku dinamičku izdržljivost, otpornost na koroziju, čvrstoću pri povišenim i visokim temperaturama, potpunu prokaljivost (95% martenzita u jezgri), laku obradljivost odvajanjem čestica, sposobnost zavarljivosti i toplinske obrade. U pogledu mikrostrukturnih zahtjeva nastoji se dobiti sitnozrnatu homogenu mikrostrukturu, uz izbjegavanje lokalnih heterogenosti (makrosegregacije, kristalne segregacije, uključci). Heterogenost u atomarnom i submikroskopskom području je poželjna radi jednoličnog usporavanja gibanja dislokacija.
Visokočvrsti čelici se mogu podijeliti u slijedeće skupine:
- niskolegirani niskopopušteni čelici,
- visokolegirani (Cr-Mo-V) visokopopušteni čelici,
- korozijski postojani precipitacijski očvrsnuti čelici,
- termomehanički obrađeni čelici,
- hladno oblikovani nelegirani ili niskolegirani čelici,
- maraging čelici.
- ↑ "Strojarski priručnik", Bojan Kraut, Tehnička knjiga Zagreb 2009.
- ↑ "Tehnička enciklopedija", glavni urednik Hrvoje Požar, Grafički zavod Hrvatske, 1987.
- ↑ "Specijalni čelici", skripta - Sveučilište u Zagrebu, www.simet.unizg.hr, 2011.
- ↑ [1] “Ispitivanje materijala”, doc. dr. sc. Stoja Rešković, Metalurški fakultet Sveučilišta u Zagrebu, www.scribd.com/doc, 2011.