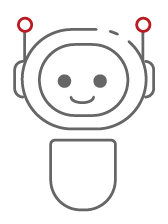
New Productive Forces, New Production Models, New Resilience
Predictions
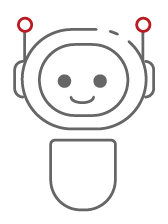
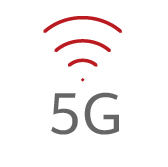

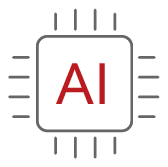
Directions for Exploration

Bringing unmanned operations to manufacturing and services to make up for labor shortages
Snapshot from the future: Collaborative robots
Collaborative robots are a type of industrial robot. They were initially designed to meet the customized and flexible manufacturing requirements of small- and medium-sized enterprises, and perfectly align with the development trends of the manufacturing industry. Collaborative robots are suitable for jobs that people don't want to do, such as highly repetitive work like sorting and packaging. Collaborative robots have several unique advantages:
Safer: Collaborative robots are compact and intelligent, and their sophisticated sensors enable them to stop in an instant.
Faster and more flexible deployment: Traditional industrial robots require professionals to plan and program their movement paths and actions, so they take a long time to deploy and are very costly. In contrast, collaborative robots feature user-friendly programming, such as programming by demonstration, natural language processing, and visual guidance. They can be placed in new positions at any time, and programing and commissioning can be completed rapidly, so they can start working very quickly.
Lower total cost of ownership (TCO) and shorter payback period: The price and annual maintenance cost of collaborative robots are significantly lower than those of traditional industrial robots. The average selling price of collaborative robots has halved over the past several years.
Snapshot from the future: Autonomous mobile robots
Autonomous mobile robots (AMRs) are a key enabler to help the manufacturing industry become flexible and intelligent. They will reshape production, warehousing, and logistics processes.
On production lines, AMRs make automated and unmanned logistics possible. This includes unmanned execution; unmanned interaction between AMRs and other equipment for material collection, feeding, and unloading; and unmanned material handling.
In warehouses, AMRs implement goods-to-person picking and execute intelligent picking, movement, and stock-in and stock-out procedures. In this model, the control system receives an order and assigns an AMR, which then lifts the shelf containing the required goods, moves it to the operator console, and unloads the goods to complete the order. After picking is completed, the robot moves the shelf back to its original position.
The distribution and picking of materials are not confined to factory buildings; AMR systems can be expanded to an entire campus. For example, when goods are unloaded, robots can automatically move them into their designated warehouses. Goods will be automatically logged into and out of warehouses, and the movement of goods between factories or warehouses will be automatically registered. These functions require the robots to support outdoor autonomous navigation, using features such as laser navigation, visual navigation, and satellite positioning.
Snapshot from the future: Industrial humanoid robots
Humanoid robots are designed to have human-like forms and functions, including anthropomorphic limbs, mobility skills, sensory perception, and learning and cognition capabilities. They will likely become the most valuable carriers of ""embodied AI"". Combined with rapidly developing general artificial intelligence and AI foundation models, humanoid robots will enable machines to interoperate and interact with their environments in a more intuitive and intelligent manner, and perform a wide variety of complex tasks just like humans.
Industrial humanoid robots can flexibly carry out different operations, move agilely, and independently learn and make decisions. Unlike traditional industrial robots, humanoid robots can complete specific tasks without requiring advanced planning. They can autonomously perceive, understand, learn, and make decisions when completing production line tasks and are capable of powerful autonomous decision making, operations, and interactions. Humanoid robots can currently work in a number of positions in factories, including material handling, quality inspection, labeling, assembly, and high-risk operations.
Humanoid robots can also work around the clock without rest, meaning they can significantly improve both production output and product quality, solve the long-standing challenges caused by labor shortages, and usher in a new era of intelligent manufacturing.
Snapshot from the future: AI-powered adaptive teaching
Conventional education uses the same model to deliver the same course content to different students. AI can transform this industry by analyzing learning models and individual differences between students. This improves the quality of education and makes it possible to teach students in accordance with their aptitudes. For example, as technologies such as big data, cloud computing, Internet of Things (IoT), virtual reality (VR), and augmented reality (AR) evolve, AI-assisted education will break down learning and teaching behavior in a more granular way and build more robust and precise education models. VR and AR technologies can be used to present materials in a more engaging manner and deliver interactions that suit students' personal preferences, helping students better master their course content.
AI liberates teachers from the repetitive and tedious grading of exam papers and administration, allowing them to focus on the creative work of educational research and one-on-one communication with students. Supported by huge amounts of data generated through educational activities, AI will help teachers better understand the effectiveness of their teaching, and provide key recommendations on the most effective teaching methods and the best way to organize course content.
In schools, AI can be deployed anywhere, and can simulate the best teachers of any subject, bringing the highest-quality education and content to the most remote schools. AI-based education offers multi-channel engagement with students, including video and audio, which can help make up for the scarcity of teaching resources in some areas (for example, in understaffed schools, a teacher may have to teach four or even five different subjects). In this way, AI promotes educational equity.

New production models geared towards personalized needs
Snapshot from the future: ICT-powered flexible manufacturing
To respond to changing market conditions and set themselves apart in the face of fierce competition, companies must take the initiative and embrace new production models. That's why an increasing number of companies are looking to concepts like flexible manufacturing. Flexible manufacturing is an advanced production model characterized by on-demand production. It helps companies become more flexible and enables them to rapidly respond to ever-changing market demand. In addition, flexible manufacturing shortens the R&D cycle, cuts R&D costs, and ensures equipment is not left idle, all while reducing inventory risks and speeding up capital turnover. Therefore, it allows companies to seize market opportunities and grow sustainably. Flexible manufacturing involves the following areas:
Flexibility of product design and production line planning: After receiving an order for a new category of product, companies need to quickly conduct R&D and design, and rapidly adjust factors such as production line equipment, working procedures, processes, and batch size. This is where ICT comes in, as simulation, modeling, VR, and other ICT technologies can be used to simulate the entire new manufacturing process. This will reduce the cost of new product development and design, and support more accurate adjustment cost projections and capacity projections.
Flexibility of process: In flexible manufacturing, companies can design products based on the personalized needs of customers, or invite customers to directly participate in product design (e.g., using modular systems to enable customers to define what a product will ultimately look like). Both models require an intelligent scheduling system. Such a system will make automatic adjustments and provide an optimal production plan based on known features such as the factory's production capacity, order complexity, and delivery deadlines. After a company receives an order, the scheduling system will automatically identify all universal components, custom components, and procedures and materials required to manufacture these components. By coordinating production tasks and the provisioning of materials and tools, the scheduling system maximizes the productivity of all equipment and workers in the factory so that no component will create a bottleneck in order delivery.
Flexibility of equipment: As the number of customizations and small-batch orders increases, factories must be able to switch between production processes in real time. Conventional manufacturing equipment can generally only be reconfigured by trained engineers using specific programming devices and languages. This makes switchover processes time-consuming, and does not support the kind of rapid responsiveness that companies need. In the future, ICT technologies such as visual programming, natural language interaction, and action capture will help factories reprogram equipment quickly and easily. This will help promptly meet companies' demand for flexible manufacturing.
Flexibility of logistics: One of the keys to flexible manufacturing is modularization, through which a large number of finished components are manufactured. This requires automated ICT technology to effectively manage warehousing and logistics, which prevents omissions and other errors in the shipment process. Take furniture producers as an example. With large-scale customization, every board, decorative strip, and handle may need its own identification code or radio frequency identification (RFID) tag to facilitate automated packing and loading, and to support traceability throughout the whole transportation and distribution process.

Resilient and intelligent supply chains that help enterprises respond to crises
Snapshot from the future: Supply chain visualization powered by digital technologies
Supply chain visualization is about using ICT technology to collect, transmit, store, and analyze upstream and downstream orders, logistics, inventories, and other relevant supply-chain information, and graphically display such information. Such visualization can effectively improve the transparency and controllability of the whole supply chain and thus greatly reduce supply chain risks.
Supply chain visualization supports the tracking of materials and equipment in upstream activities. Logistics information is displayed in real time.
With supply chain visualization, the operation data of various transportation vehicles in the logistics system is also available, and the status of these vehicles can be displayed in real time. Global Positioning System (GPS), AI, 5G-A, IoT, and other technologies are used to monitor the transportation process and the status of goods while in transit. There is also a visualized scheduling center that enables the consolidation or splitting of orders at any time, and the optimization of transportation resources and routes. This enables companies to detect and rapidly respond to any logistics emergency by promptly adjusting logistics routes to ensure the timely and safe delivery of goods.
A remote monitoring system monitors the environment in warehouses in real time. This system uses various sensors to graphically display operations and maintenance (O&M) information such as temperature, humidity, dust, and smoke. This allows the timely detection of any signs of fire or water leakage, enabling prompt intervention and preventing material losses. Goods can also be tracked in real time as they are logged into and out of warehouses. As goods are moved, IoT, RFID, and QR code technologies are used to automatically identify and register goods, and the warehousing status data of goods can be accessed remotely in real time.
Snapshot from the future: From supply chain to supply network
In the traditional supply chain model, each link in the chain depends on the previous link delivering as expected. Each link could be a bottleneck that prevents the normal flow of goods down the chain. For example, if the supply of an upstream raw material provider is disrupted, downstream manufacturers will definitely be affected, resulting in inefficient operations or even a standstill for the entire supply chain. With the adoption of ICT technologies such as cloud computing, IoT, big data, and AI, the supply chain will transform into a supply network. In this network, the upstream materials required by every link have multiple alternative sources, and they can be sourced through multiple routes. A multi-contact collaborative supply ecosystem will be created by enhancing the internal and external interconnectivity of enterprises. The failure of any single link will not paralyze the entire supply network.
More Outlooks
