Abstract
The world heritage object Nebra Sky Disc is one of the best investigated archaeological objects. The origin of the raw materials it is made of is well known. However, its manufacturing process was not completely clear. Investigations were made in order to clarify the steps of manufacturing from the initial casting to the finished disc using the latest metallographic techniques. Therefore, a small piece from the outer part of the disc was investigated and compared with a replica. Both were prepared regarding the metallographic procedure. Microstructural analysis was made by optical microscopy on a colour etched surface, EDS and electron backscatter diffraction. For the investigation of mechanical properties microhardness measurements were made. It could be found that the Nebra Sky Disc was manufactured from a flat cast followed by hot forging process. During the forging process the disc was heated and forged for approximately 10 times.
Similar content being viewed by others
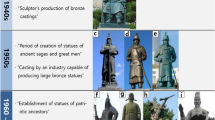
Introduction
The Nebra Sky Disk is the oldest precise depiction of the heavens in human history (Fig. 1). It is inscribed on the UNESCO Memory of the World Register and is one of the most thoroughly studied archaeological objects in the world, because its cosmological iconography offers a unique insight into the mind set of Early Bronze Age people. It was discovered and looted by unlicensed metal detectorists on the summit of the Mittelberg hill near the town of Nebra, Saxony-Anhalt, in central Germany in 19991,2. The disc was included in a hoard which included two superbly crafted swords, two flanged axes, two spiral bracelets and a chisel. The associated finds date the deposition of the Sky Disc to the end of the central European Early Bronze Age, ca. 1600 BC. However, it is highly likely that the Sky Disc itself had been manufactured some 100 to 200 years earlier. From technical observations, as well as the analysis of the gold inlays, a five-phase reconstruction of the development of the imagery on the disc seems to be the likeliest sequence for the discâs development. In the earliest version, an elaborately encoded image reflects sophisticated astronomical knowledge. In subsequent stages this was forgotten and replaced by traditional knowledge, which was focused on the interaction of the heavenly bodies and the horizon; and finally, this reduced knowledge gave way to mythology2,3,4. Besides the changes to the motifs, the origins of the raw materials it was made from, copper, tin and gold, are also well understood5,6,7,8.
The chemical composition of the base material refers to an early bronze. Besides copper, the disk contains mostly tin (2.6 ma. %) and some nickel (0.22 ma. %), zinc (0.15 ma. %) and arsenic (0.21 ma. %)5. However, the specific steps involved in producing the disk are still the subject of speculation. It can be ruled out that the disc is a cast product, as the limited flow behaviour of the molten metal could not form such a thin disc9. It was determined that the disk was in fact produced by alternately hot forging a cast preform10,11,12,13. Forging was carried out step by step spiraling from its centre to the rim. The hot forging of a bronze with this chemical composition of the Sky Disc is limited to a fixed parameter setting with regard to temperature and maximum deformation14.
The clarification of the exact manufacturing process was the aim of this study. Therefore, the Nebra Sky Disc was metallographically investigated using the latest methods. Furthermore, several replicas of the Nebra Sky Disc were manufactured and analysed as well (Fig. 2). The replicas represent different stages of the manufacturing process from the cast preform over rising degree of deformation. The comparison of the microstructure of the original Nebra Sky Disc with the replicas provides detailed information on the manufacturing process.
Results
The Nebra Sky Disc
During the first investigation of the Nebra Sky Disc5 a small piece was cut out as can be seen in Fig. 1. This piece was used for the metallographic analysis of this work. It was not possible to take further samples from different areas of the disc because of its outstanding importance. But the sampled location represents an area of maximal treatment, especially a high deformation degree, if the disc is made by forging a preform. For this reason, it is appropriate to investigate the manufacturing process. Different techniques were used for the microstructural characterisation. The results are summarised in Fig. 2. It can be seen that the microstructure of the Nebra Sky Disc is characterised by medium sized grains with annealing twins. The element distribution, especially the tin distribution is inhomogeneous. Elongated particles can be found in the microstructure. EDS measurements identify them as Sulphides, Fig. 3. These inclusions are mostly elongated and line-like arranged. Furthermore, there are defects as gaps and deformed holes. The smooth pathway of the defects refers not to cracks but to imperfections from the casting.
The results from the microstructural analysis led to the assumption, that the Nebra Sky Disc was made by forging a casted preform in combination with a heat treatment. The casting probably had a dendritic microstructure, inferred by the inhomogeneous tin distribution, with some casting defects. During the forging defects were deformed and compressed and the primarily homogeneous distributed inclusions rearranged in lines. The forging initiates a high number of dislocations. A subsequent heat treatment led to the formation of new grains and the microstructure transforms from dendritic to granular. The formation of annealing twins is characteristic for recrystallized face-centre cubic metals with low stacking fault energy, as copper. The final step of the manufacturing process seems to be a heat treatment because the grains are randomly orientated.
This theory of the manufacturing of the Nebra Sky Disc, which was deduced from the microstructure, will be verified by manufacturing of replica discs subsequently.
Replica manufacturing
The thickness of the Nebra Sky Disc is between 4.6Â mm (centre) and 1.5â1.8Â mm on its edge. The manufacturing process of a bronze disc is complex, because of its materials characteristics. Without the modern techniques of materials processing, manufacturing of such a disc in the Bronze Age was challenging. The material has a poor castability because of its low content of tin and arsenic. Thatâs why, a cast of a thin disc of bronze seems not to have been feasible. This is the reason why it is assumed that the Nebra Sky Disc was manufactured by forging a casted preform. The significant change in geometry from the preform to the disc needs an experienced coppersmith because the work must be done manually. Before the manufacturing of the replica, it was necessary to acquire experiences in the materials handling. The necessary force for forging decreases and the maximum deformation degree of bronze rises with an increasing temperature. The forging was performed by helical hammer strokes moving outwards from the centre. During the hot forging the materials temperature and the formability decrease. Therefore, it seems to be consistent that within the Bronze Age a bronze disc could only be produced by alternating (hot) forging and heating.
For replica manufacturing a chemical composition corresponding to the Nebra Sky Disc was chosen5. The melt consists of tin (2.56 wt%), iron (0.16 wt%), nickel (0.22 wt%) and zinc (0.15 wt%, rest copper). There was no addition of noxious arsenic, which was detected in the Nebra Sky Disc. A significant impact on the mechanical properties needs an arsenic content of over 4 wt.%15 and the Nebra Sky Disc only contains 0.21 wt% arsenic. So, the influence of arsenic on the results of this study was considered to be negligible. Sulphur is excluded too, although the microstructural analysis proofs the existence of sulphides. The materials composition was measured by X-ray fluorescence, which is not able to measure Sulphur. Furthermore, the existence of Sulphides, in the amount evident from the microstructural analysis, was considered not to influence the formability.
Some preforms were casted and used for a first study to find an appropriate process route of smithing this alloy. Although the materials composition is supposed to have a good cold formability, it was found that the required deformation degree is too high to convert the preform in the disc replica only by cold forming. It took several trails to find a practicable way of forging the disc without crack propagation. It was found that this takes a numerus cycles, each consisting of heating to nearly 700 °C immediately followed by helical hammer forging (Fig. 4) to deform the casted preform into a disc. The forging converts the geometry stepwise from the preform to the disc. Thereby the formability decreases. Intermediate heating increases the formability. During the smithing the compact preform is converted in a thin disc, the diameter increases significant. The coppersmith used different hammers for the work. At the beginning he used a hammer weighing 5 kg, while after a few cycles the weight of the hammer was reduced to 2 kg, 1.5 kg and 1.1 kg respectively. For forging the rim, he used a small hammer with a round, slightly curved face and a weight of only 0.63 kg. The helical hammering is necessary to shift the materials volume from the bulky centre. Figure 5 shows the four replicas of our study. Each represents a single step of the manufacturing process: (a) the cast preform, (b) intermediate stage 1 (heated and forged, 1 cycle), (c) intermediate stage 2 (heated and forged, 10 cycles), and (d) disc (heated and forged, 55 cycles, finalised by an annealing treatment at nearly 750 °C for 10 min).
The lens-shaped preform with a diameter of 130 mm and a thickness of 30 mm was made by open sand casting16. Before each forging operation the material was heated to reduce the necessary forces and to increase the formability. Stage 1 shows the impact areas from the hammer, which struck the surface in a spiral movement from the inside to the outside. Thereby, the cast became flat and wide. Because of the work hardening, the formability is limited. The necessary deformation degree can only be reached by intermediate annealing. The annealing temperature is estimated by the experience of the coppersmith from the temper colour. An interim measurement by pyrometer showed that the temperature of the replicas was around 700 °C. During the subsequent hot forging the material cooled down. Consequently, the necessary forming forces increased, and the formability decreased. The coppersmith registered that by the necessary force, he needed to deform the material. To prevent crack formation forging had to be stopped at a certain temperature. It is not possible to define an exact value for the minimum temperature necessary for manual forging, because it is influenced by several conditions (chemical composition, local deformation degree, local temperature etc.). Thus, the workflow depends on the experience of the coppersmith. Stage 2 shows this process after being repeated 10 times, resulting in a flatter and wider shape. The deformation degree is around 0.5. It took 55 cycles of heating and forging to form the stage 3 (final disc), with a deformation degree of circa 0.85. The shape of the replica is identical with the original Nebra Sky Disc (diameter: 315â320 mm, thickness: 4.5 mm in the centre and 1.7 mm outside4). The last step of the materials treatment is a stress relief heat treatment to reduce internal stresses.
Microstructure
The microstructural analysis of the different replica stages from the initial cast to the finished disc and the microstructure of the Nebra Sky Disc can be seen in Fig. 6.
The comparison of the replica stages shows the development of the microstructure resulting from the manufacturing process (heating and forging). The cast sample has a regular, coarse-grained microstructure of primary dendrites and interdendritic spaces. The colour etching indicates a gradient in the local chemical composition. Small inclusions are dispersed. Furthermore, shrinkage cavities can be found. The dendritic microstructure, inclusions and the shrinkage cavities can also be found in the stage 1. The first cycle of heating and forging disturbed the regular composition of the as-cast microstructure but has no further significance. The composition gradient is conserved. Stage 2 shows a distinct development of the microstructure resulting from the repetition of heating and forging. The coarse-grained dendrites transform to a structure of medium sized, globular grains. The forging increases the dislocation density and during the following heating a recrystallization is initiated. This also leads to the presence of annealing twins and a regular subgrain structure. The gradient in local chemical composition as well as shrinkage cavities can still be found but they are strongly decreased by the manufacturing process. An effect of the distribution of the inclusions could not be found. The microstructure of the stage 3 consists of globular coarse grains with annealing twins. The chemical composition is homogenised. The inclusions are redistributed during the forging, so that they are arranged in lines.
The microstructure of the original Nebra Sky Disc consists of medium sized grains with annealing twins, as can be seen also in Fig. 4 (grain boundary etched picture). Shrinkage cavities can be found as well as a long gaps. The colour etched picture indicates a moderate inhomogeneous distribution of alloying elements.
Tin distribution
An important indication for a hot forming process of bronze is the tin distribution. The colour etched surfaces of the micrographs indicate differences between the tin distribution of the investigated samples. For further investigation energy-dispersive X-ray spectroscopy (EDS) was made. Figure 7 shows the results.
The cast replica shows the expected strong inhomogeneous tin distribution, resulting from the solidification during the casting process. First primary Cu dendrites solidify in the melt starting from crystal nucleus. The tin solubility in the Cu dendrites is limited. As the dendrites grow, tin is enriched in the interdendritic space, which solidifies as last. This can be seen from the EDS map of the cast replica. The replica stage 1 also shows this inhomogeneous tin distribution. The first cycle of heating and forging did not affect the tin distribution. For the stage 2 it can be found that the space between the tin enriched spaces became smaller. This results from the repeated forging, which compresses the microstructure. For the stage 3 the results of EDS measurements prove a homogeneous tin distribution. The repetition of heating and forging led to a homogeneous distribution of the alloying elements.
The sample of the Nebra Sky Disc shows a tin distribution comparable with the replica stage 2. The tin enriched spaces are smaller as it would be for a cast bronze.
Lattice and texture
In addition to the optical microscopy the microstructures were also analysed by Electron Backscatter Diffraction (EBSD). In addition to the optical microscopy EBSD gives information on the lattice orientation of grains and texture. The comparison in Fig. 8 shows the results for the replica stages and the Nebra Sky Disc.
The EBSD map of inverse pole figures (IPF) of the cast replica shows a coarse grain structure. The calculation of the average grain size is not possible, because not enough grains were completely mapped. This is also the case for the results of the optical microscopy. There is no misorientation within the coarse grains, which corresponds to the as cast condition. The texture measurement is not representative for the materials texture, because there are less grains for calculation. The IPF map of stage 1 shows only few grains referring to a coarse microstructure, as well. A calculation of the average grain size is not possible because there are less grains, and thus the texture measurement is not representative. However, it is possible to see a misorientation within the grains. This corresponds to the first manufacturing step of the material. During the forging dislocations are generated and the grains are deformed. The subsequent heating in combination with a small degree of deformation is insufficient to anneal the deformation or to recrystallise smaller grains. Stage 2 shows a medium sized grain with annealing twins. The average grain size, calculated from the EBSD data without twins, is 70 μm. The grain orientation is random. The texture measurement indicates a recrystallisation. In this stage, the repetition of forging and heating has significant influence on the microstructure. During forging dislocations are generated and increased the critical deformation degree for recrystallisation, which is necessary to form new grains, is accomplished. The subsequent heating led to the formation of small new grains and the microstructure recrystallises. Thus, the microstructure of stage 2 is finer than stage 1. Stage 3 has a much coarser microstructure with an average grains size of 233 μm. The texture map shows single maxima and no clear recrystallisation texture. However, this result is not reliable because there is an insufficient number of grains for such a calculation. It is supposed that the deformation degree during the final forging was too low for the initiation of recrystallisation during the final heating. So, the growth of existing grains was preferential, and the microstructure became coarse.
The EBSD data from the original Nebra Sky Disc show medium sized and random oriented grains with annealing twins and a recrystallisation texture. The grainsize is 65 μm. The microstructure of the Nebra Sky Disc is comparable to the stage 2 replica. The outcome of this result is, that the final manufacturing step of the Nebra Sky Disc consisted of forging with a high deformation degree, followed by a recrystallisation heat treatment.
Microhardness
The mechanical properties of the samples were measured by micro hardness testing. The results are shown in Fig. 9. A varying influence of main alloying elements on the hardness can be excluded, because the investigated samples have nearly the same chemical composition. Thus, only the manufacturing process can influence the mechanical properties.
The hardness of the cast replica is 64 HV0.1, which corresponds to a usual cast bronze with low tin content. The replica stage 1 has a somewhat higher hardness (66 HV0.1) as the cast sample. The difference of only 2 HV0.1 is too low to be doubtlessly caused by forging. But in combination with the results from the microstructural analysis an influence of the manufacturing process can be expected. A distinct influence of the manufacturing can be seen in the significantly higher hardness of the replica stage 2 (76 HV0.1). The hardness results from the small grain size. During the forging and heating recrystallisation took place, resulting in a fine-grained microstructure. The hardness increases by fine grain hardening. The tin segregation has no influence on the hardness, which can be seen from the small spreading of the hardness values. The stage 3 has the lowest hardness (52 HV0.1) of all samples, caused by the coarse-grained and annealed microstructure.
The Nebra Sky Disc shows the highest hardness (79 HV0.1) of the samples. This results from the smaller grain size of the Nebra Sky Disc. Due to the recrystallisation an decreasing grain size led to increasing hardness. The hardness is the same than it was measured for the replica stage 2.
Discussion
The Nebra Sky Disc is an impressive reflection of the profound astronomical knowledge of the Early Bronze Age ÃnÄtice culture in central Germany. Moreover, it proves the existence of an advanced understanding of metals treatment during this early period. The manufacturing of this disc differs from the making of other artefacts from the Early Bronze Age, e.g. the bronze axes. To be fit for purpose, axes must have a high hardness in the cutting edge. Due to the low tin content of most axes in the Early Bronze Age, production focussed on work hardening17. Ornaments or ritual objects had to be durable and visually appealing. Sheet metal ornaments, which are especially found in the regions along the Danube, are basically comparable to the Sky Disc in the way of production, but they are much smaller and thinner18,19. Extending a cast bronze preform to a disc of 4.6 to 1.5â1.8Â mm thickness, requires a complex sequence of heating and forging.
The aim of this work was to clarify the manufacturing process of the Nebra Sky Disc. The comparison of microstructural properties of the Nebra Sky Disc and different replicas, each of which represents a step of the possible manufacturing process, allows the identification of analogies and gives evidence on the knowledge of the smith of the Nebra Sky Disc.
The observations made on the replica represent the microstructural evolution of a bronze during the treatment. Casting of the bronze is the first step. The fluidity of the melt is limited and inhibits the manufacturing of the disc only by casting. Thus, it is necessary to cast a preform. During this stage the microstructure consisted of coarse-grained dendrites. Because of the low solubility in the dendrites, tin enriches in the interdendritic spaces. Even this preform shows microstructural defects (shrinkage cavities), which is a symptom of the limited fluidity of the melt.
Consequently, the cast preform must be forged if a thin disc is the desired result. Forging leads to the formation of dislocations and deformation inside of grains. With increasing deformation, the number of dislocations rises as the interaction between them. Dislocations block the movability of each other, which lead to a limited macroscopic deformation behaviour of the material (work hardening). That is the reason why the deformation behaviour of bronze is limited at room temperature. The high deformation degree, which is necessary to extend the disc from its preform, can only be reached by an alteration of forging in combination with a heat treatment. Due to an annealing treatment, dislocations are depleted and the formability increases. Furthermore, the strength of the material decreases with the increase in the materialâs temperature. Hence, it is consistent to expect that the coppersmith combined the annealing with the forging of the hot metal, because of the lower forming forces and higher formability of the material. During this process the metal cools down, so the annealing must be repeated several times to reach the desired disk´s shape.
The influence of this process on the microstructure can be seen from the investigated replica during different stages of hot forging. The cast consists of coarse-grained dendrites. After the first cycle the thickness of the sample is slightly reduced by plastic deformation. The microstructure can be still characterized as dendritic, with compressed dendrites. The local tin enrichment is conserved, as well as the shrinkage cavity. For this reason, the materialâs hardness is nearly the same as was measured for the cast sample. The repetition of heating and forging changes the object´s microstructure. The forging increases the local dislocation density, which serve as nucleus for recrystallisation processes. During the heat treatment many new grain boundaries form (recrystallisation heat treatment). Hence, the grain size of the material is reduced. As a result, the materials hardness increases (fine grain hardening). The shrinkage cavities are compressed due to the forging. The tin distribution becomes as more homogeneous as the hot forging is repeated. After the last forging step, the material is reheated (stress relief heat treatment), which is indicated by the random grain orientation and annealing twins. This is done to reduce the internal stresses and prevent brittle cracking. A bronze axe needs internal stress in order to reach high hardness and a enable a strong cutting edge. For the Nebra Sky Disc there are no requirements on mechanical properties but instead on the persistence and dimensional stability. Furthermore, it is necessary to restore the formability, because of the further treatment. The golden inlays on the surface of the disc are made by damascening, which requires local material deformation. Thus, a stress relief heat treatment after the final forging is a reasonable, even if the exact temperature-time regime was probably not hit during our investigations, resulting in clearly enlarged grains within the replica disc. Overall, replica step 2 is the most similar to the original disc.
Comparing microstructures of the different replica stages with the Nebra Sky Disc allows us to infer the manufacturing process of the UNESCO world heritage document. It must be noted that the replica manufacturing was a manual work, based on the experience of the coppersmith. It is neither possible nor the aim to rebuild the Nebra Sky Disc with strict and defined parameters. The Nebra Sky Disc is the result of the manual work of an experienced coppersmith. Thatâs why it is consistent to rely on an experienced coppersmith to make the replicas. It is not possible to infer the single steps of the Nebra Sky Disc manufacturing in every single detail because of the plurality of parameters. However, this study revealed the basic processing. The microstructural characteristics (grain size, grain orientation, texture, microhardness, tin distribution and morphology of shrinkage cavities) of the Nebra Sky Disc validate our reconstruction of the manufacturing process. The fine-grained structure is the result of an alternating hot forging of a cast preform.
Further, it was shown that the microstructure of the Nebra Sky Disc does not correspond to the final replica disc (stage 3). The larger grain size of the replica could correspond to a low deformation degree in the late stage of manufacturing, resulting in a grain coarsening instead of a fine grain recrystallization during the heating. Furthermore, there is a homogeneous tin distribution in the replica. This indicates that the overall deformation degree of stage 3 is higher than that of the original disc, which shows an inhomogeneous tin distribution.
Surprisingly, the microstructure of the replica stage 2, instead of replica stage 3, is similar to the Nebra Sky Disc regarding all microstructural properties. This leads to the assumption that the preform was thinner with a higher diameter than we have chosen for the cast replica. Hence, the necessary repetition of the hot forging for forming of the disc is lower and the inhomogeneous tin distribution, resulting from the casting, is reduced but not eliminated.
It is already known that the Nebra Sky Disc was finished after forging by damascening the inlays and, probably, a patination of the surface12,20. Based on this new microstructural investigation it is now possible to understand the process of the manufacturing of the bronze disc as well. The result demonstrates the importance of forging in Bronze Age metallurgy, which is often seen and researched mainly from the perspective of metal casting.
The Nebra Sky Disc is an extraordinary relict of the Early Bronze Age and an impressive example of the profound knowledge that was available in the ÃnÄtice culture. Since it proves a detailed understanding of astronomic correlations, it became UNESCO Memory of the World. Furthermore, its manufacture was by no means trivial. While the production of axes and sheet metal jewellery by forging techniques were common practice in the Central European Early Bronze Age13,17,18,19,21, the Nebra Sky Disc is, according to current knowledge, unique in its shape, size and volume. The influence of the ÃnÄtice culture on Early Bronze Age metallurgy has been often discussed, with a particular focus on innovative casting techniques22. In this context, the Nebra Sky Disc documents, that the ÃnÄtice culture craftsmen were excellent and innovative copper smiths with extensive experience in sophisticated bronze manufacturing, including casting, forging and heat treatment.
Methods
Optical microscopy
For the optical microscopy microsections were made. Therefore, small pieces were cut out of the disc. For stage 1 and stage 2 the samples were taken near the surface where the area impacted by the hammer had an influence on the microstructural development. The sample of the replica disc originates from the similar position as the piece of the original Nebra Sky Disc.
Following exploratory experiments, a small approximately square block sample (5Â mm wide) was extracted by the electroerosion method from the original Nebra Sky Disc already in 200223,24. This sample was used for metal analyses5 [Per10] and the first11 as well as the recent metallographic analyses.
The microsections were ground and polished. For etching two different etchants were used. For contrasting the grain boundaries, the microsections were etched with a solution of hydrochloric acid and iron (III) chloride. The colour etching according to Klemm visualises gradients in chemical composition.
Electron microscopy
For the SEM-Analysis the microsections were repolished. As final polishing step alumina suspension with addition of hydrogen peroxide was used. This resulted in virtually scratch- and deformation-free surfaces.
Energy dispersive X-ray spectroscopy
EDS measurements were performed to analyse inclusions and the chemical gradients shown in the colour etched microsections. The EDS measurements were done at 20 kV on the polished microsections. For the EDS maps an area of 354âÃâ275 μm were scanned. To apply electrical contact the samples were sputtered with Gold (Au). The EDS measuring signals for Au were neglected for the analysis.
Electron backscatter diffraction
For EBSD the fine polished microsections were tilted to 70° in the SEM. An area of 354âÃâ275 μm were scanned with a step size of 0.8 μm. The electron beam was set to 20 kV. The binning of the CCD camera was set to 5âÃâ5 to optimize the scan speed while keeping the quality of the pattern. The EBSD pattern were post processed via reindexing and averaging of neighbour pattern.
The EBSD datasets were visualized as inverse pole figure (IPF) colour coded and Confidence Index (CI) grey scaled maps. Furthermore, texture analysis was performed as Harmonic Texture Expansion. The harmonic texture plots are shown as pole figure.
Hardness measurement
The hardness of the samples was measured by microhardness. The Vickers test with a load of 0.980Â N (HV0.1) was used as the method in accordance with EN ISO 6507-1:2018.
Due to the small available test area on the microsection of the Nebra Sky Disc, as well as to avoid deeper deformation and alteration of the specimen, the microhardness test was used.
Data availability
The data that is necessary to interpret, verify and extend the research in the article is published in the current paper.
References
Meller, H. Die Himmelsscheibe Von NebraâEin frühbronzezeitlicher Fund Von auÃergewöhnlicher Bedeutung. Archäologie Sachsen-Anhalt N F. 1, 7â20 (2002).
Meller, H. & Nebra Vom Logos Zum MythosâBiographie eines Himmelsbildes in Der Griff Nach Den Sternen. Wie Europas Eliten zu Macht Und Reichtum Kamen (eds Meller, H. & Bertemes, F.) 23â73 (Landesamt für Denkmalpflege und Archäologie SachsenÂ-Anhalt, 2010).
Meller, H. The Sky Disc of Nebra. In The Oxford Handbook of the European Bronze Age (eds Fokkens, H. & Harding, A.) 266â269 (Oxford University Press, 2013).
Meller, H. Die Himmelsscheibe Von Nebra â Ein Physischer Atlas. Technische Und Naturwissenschaftliche Beobachtungen (Landesamt für Denkmalpflege und Archäologie SachsenÂ-Anhalt, in preparation).
Pernicka, E. Archäometallurgische Untersuchungen am und Zum Hortfund Von Nebra, in Der Griff Nach Den Sternen. Wie Europas Eliten zu Macht Und Reichtum Kamen (eds (eds Meller, H. & Bertemes, F.) 718â734 (Landesamt für Denkmalpflege und Archäologie SachsenÂ-Anhalt, (2010).
Haustein, M., Gillis, C. & Pernicka, E. Tin isotopyâa new method for solving old questions. Archaeometry 52, 816â832 (2010).
Nessel, B., Brügmann, G. & Pernicka, E. Tin isotope ratios in early and middle bronze age bronzes from central and southeastern Europe. UISPP J. Int. Union Prehistoric Protohistoric Sci. 2, 1â11 (2019).
Borg, G. et al. From distant landsâprovenance studies of natural gold in comparison to the gold of the Sky Disc of Nebra. In Der Aufbruch zu Neuen Horizonten. Neue Sichtweisen Zur europäischen Frühbronzezeit (eds Meller, H. & Bertemes, F.) 55â78 (Landesamt für Denkmalpflege und Archäologie SachsenÂ-Anhalt, 2019).
Fritz, A. H., Schulze, G. & Urformen. In Fertigungstechnik (eds Fritz, A. & Schulze, G.) 5â114 (Springer, 2010). https://doi.org/10.1007/978-3-642-12879-0_2
Berger, D., Schwab, R. & Wunderlich, C. H. Technologische Untersuchungen zu Bronzezeitlichen Metallziertechniken nördlich Der Alpen Vor dem Hintergrund Des Hortfundes Von Nebra. In Der Griff Nach Den Sternen. Wie Europas Eliten zu Macht Und Reichtum Kamen (eds Meller, H. & Bertemes, F.) 751â777 (Landesamt für Denkmalpflege und Archäologie SachsenÂ-Anhalt, 2010).
Nickel, D., Pernicka, E., Klare, H. & Triebel, J. Metallkundliche Untersuchungen. In Die Himmelsscheibe von NebraâWeitere archäologische und naturwissenschaftliche Studien (ed Heller, H.) (Landesamt für Denkmalpflege und Archäologie SachsenÂ-Anhalt, accepted).
Wunderlich, C. H. Spuren aus der Zeit der Herstellung der Himmelsscheibe. In Die Himmelsscheibe von NebraâEin physischer Atlas. Technische und naturwissenschaftliche Beobachtungen (ed Meller, H.) (Landesamt für Denkmalpflege und Archäologie SachsenÂ-Anhalt, accepted).
Kienlin, T. L. Traditions and Transformations: Approaches to Eneolithic (Copper Age) and Bronze Age Metalworking and Society in Eastern Central Europe and the Carpathian Basin (Archaeo, 2010).
Kupfer-Zinn-Knetlegierungen (Zinnbronzen). Informationsdruck i.15 (especially page 16) (Deutsches Kupferinstitut, 2004).
Neukirch, F. Von Der Kupfersteinzeit Bis zu den Seltenen Erden: Eine Kurze Geschichte Der Metalle (Springer Spektrum, 2016).
Bauer, H. R. & Schmiedeexperimente. In Die Himmelsscheibe von NebraâEin physischer Atlas. Technische und naturwissenschaftliche Beobachtungen (ed Meller, H.) (Landesamt für Denkmalpflege und Archäologie SachsenÂ-Anhalt, accepted).
Michael, O. et al. Archaeometallurgical investigations into the production of early and middle bronze age flanged axes in Central Germany. In The Social Value of Prehistoric axes: New Archaeological and Archaeometric Approaches (eds Risch, R., Pernicka, E. & Meller, H.) 467â478 (Landesamt für Denkmalpflege und Archäologie SachsenÂ-Anhalt, 2024).
Neugebauer, C. & Neugebauer, J. W. Franzhausen. Das frühbronzezeitliche Gräberfeld I (Berger, 1997).
Massy, K. Die Gräber Der Frühbronzezeit Im südlichen Bayern. Untersuchungen zu den Bestattungs- und Beigabensitten Sowie gräberfeldimmanenten Strukturen (Verlag Michael Lassleben, 2018).
Berger, D. Bronzezeitliche Färbetechniken an Metallobjekten nördlich Der Alpen. Eine archäometallurgische Studie Zur prähistorischen Anwendung Von Tauschierung Und Patinierung Anhand Von Artefakten Und Experimenten (Landesamt für Denkmalpflege und Archäologie SachsenÂ-Anhalt, 2012).
Kuijpers, M. H. G. An Archaeology of Skill. Metalworking Skill and Material Specialization in Early Bronze Age Central Europe (Routledge, 2018).
Schwenzer, S. Zum Einfluss Der Aunjetitzer Kultur auf die frühbronzezeitliche Metallverarbeitung in Mitteleuropa. Archäologisches Korrespondenzblatt 34, 193â210 (2004).
Pernicka, E., Nickel, D. & Wunderlich, C. H. Probenahmen am Hortfund von Nebra, in Die Himmelsscheibe von NebraâWeitere archäologische und naturwissenschaftliche Studien (ed Heller, H.) (Landesamt für Denkmalpflege und Archäologie SachsenÂ-Anhalt, accepted).
Wunderlich, C. H. & Restaurierung. In Die Himmelsscheibe von NebraâEin physischer Atlas. Technische und naturwissenschaftliche Beobachtungen (ed Meller, H.) (Landesamt für Denkmalpflege und Archäologie SachsenÂ-Anhalt, accepted).
Acknowledgements
The authors thank the MDZWP e.V. for supporting the measurement of microhardness and L. D. Nebelsick for improving the language.
Author information
Authors and Affiliations
Contributions
S. Dieck interpretated and concluded the results of the metallurgical investigations and wrote the part of the article regarding materials science. O. Michael realised the metallurgical investigations (preparation, optical and electron microscopy). M. Wilke and T. Halle contributed appropriate methods of investigation and important approaches of interpretation of the correlation between the investigated microstructure and possible smithing process, causing in this microstructure. C.-H. Wunderlich designed the replica manufacturing as well as its preliminary steps and discussed the experiments and their results intensively with Herbert R. Bauer. J.-H. Bunnefeld wrote the archaeological part of the manuscript.Herbert R. Bauer realised the copper smith work of the replica manufacturing. Besides the replica, which are presented in this article, his work included numerous preliminary work to find the right conditions for smithing the chosen alloy. H. Meller contributed substantially to the conceptualisation of the study and provided funding.All authors revised the manuscript.
Corresponding authors
Ethics declarations
Competing interests
The authors declare no competing interests.
Additional information
Publisherâs note
Springer Nature remains neutral with regard to jurisdictional claims in published maps and institutional affiliations.
Rights and permissions
Open Access This article is licensed under a Creative Commons Attribution-NonCommercial-NoDerivatives 4.0 International License, which permits any non-commercial use, sharing, distribution and reproduction in any medium or format, as long as you give appropriate credit to the original author(s) and the source, provide a link to the Creative Commons licence, and indicate if you modified the licensed material. You do not have permission under this licence to share adapted material derived from this article or parts of it. The images or other third party material in this article are included in the articleâs Creative Commons licence, unless indicated otherwise in a credit line to the material. If material is not included in the articleâs Creative Commons licence and your intended use is not permitted by statutory regulation or exceeds the permitted use, you will need to obtain permission directly from the copyright holder. To view a copy of this licence, visit http://creativecommons.org/licenses/by-nc-nd/4.0/.
About this article
Cite this article
Dieck, S., Michael, O., Wilke, M. et al. Archaeometallurgical investigation of the Nebra Sky Disc. Sci Rep 14, 28868 (2024). https://doi.org/10.1038/s41598-024-80545-5
Received:
Accepted:
Published:
DOI: https://doi.org/10.1038/s41598-024-80545-5