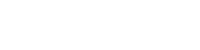
E5 | Medicine Cabinet, Chimney Crown | Ask This Old House
Season 23 Episode 5 | 23m 42sVideo has Closed Captions
Nathan installs a bathroom recessed cabinet; Mark repairs a chimney crown.
Nathan Gilbert transforms a homeowner's hanging bathroom medicine cabinet into a recessed medicine cabinet; Mark McCullough replaces a chimney crown that is causing water damage to a homeowner's indoor charcoal grill; Mark shows Kevin O'Connor some of the little pieces of history he's found while doing masonry work over the years.
Funding for THIS OLD HOUSE is provided by The Home Depot and Renewal By Andersen.
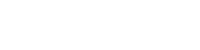
E5 | Medicine Cabinet, Chimney Crown | Ask This Old House
Season 23 Episode 5 | 23m 42sVideo has Closed Captions
Nathan Gilbert transforms a homeowner's hanging bathroom medicine cabinet into a recessed medicine cabinet; Mark McCullough replaces a chimney crown that is causing water damage to a homeowner's indoor charcoal grill; Mark shows Kevin O'Connor some of the little pieces of history he's found while doing masonry work over the years.
How to Watch Ask This Old House
Ask This Old House is available to stream on pbs.org and the free PBS App, available on iPhone, Apple TV, Android TV, Android smartphones, Amazon Fire TV, Amazon Fire Tablet, Roku, Samsung Smart TV, and Vizio.
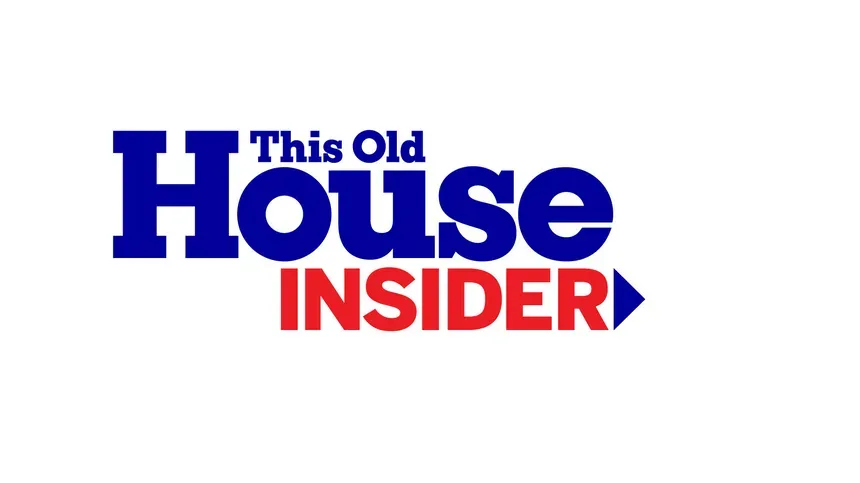
This Old House Insider Newsletter
Get This Old House exclusive stories, tips, and behind-the-scenes information delivered right to your inbox every month.Providing Support for PBS.org
Learn Moreabout PBS online sponsorship♪♪ Kevin: On "Ask This Old House," our experts travel across the country to answer questions about your house.
♪♪ Today Nathan helps a homeowner install a recessed bathroom cabinet.
Then Mark replaces a homeowner's chimney crown.
Mark: That looks beautiful.
Kevin: And Mark also shares a few treasures he's found over the years.
Oh, there's a note inside.
Mark: There is.
Kevin: Did you read it?
Mark: I had to.
I couldn't resist.
Kevin: On "Ask This Old House."
♪♪ Kyle: Thanks for coming, Nathan.
Nathan: Thanks for having me.
Kyle: My wife and I have been remodeling, and one of the things that we wanted to replace is the medicine cabinet in our bathroom.
Nathan: All right.
Let's take a look It's right in here.
Nathan: All right.
This is the medicine cabinet.
Kyle: Yeah.
Nathan: All right.
Kyle: So it's a little bit bulky, a little bit outdated, and a little bit beat up.
So we were looking for something a bit more modern that we could recess into the wall.
But it being a bathroom and going to the wall, with lighting and plumbing and not knowing if it's load-bearing -- I know I sent over some photos.
Nathan: Yeah.
Those photos are extremely helpful.
With those photos, I was able to tell that the rafters fly by and that this is not a load-bearing wall.
So we know we can nip and tuck it.
Other things to be cautious of, like you said, electrical behind here, maybe a vent coming out of the sink.
So we want to go nice and slow, make an opening, and check it.
I think we can definitely do it.
So let's get some tools and get started.
Kyle: Sounds great.
Thanks.
Nathan: The first step is to take down the old medicine cabinet.
All right.
So I'm gonna pull these two top screws out.
And then I'll hop down and we'll pull the bottom two screws.
Here we go.
Nice.
So now that we have the medicine cabinet off, what I'd like to do is actually do the layout of the whole cabinet that you picked out.
Then I'd like to make a small little pilot hole between these studs, make a little hole I can open up and look and see if there's electrical.
Maybe I can reach in and see if there's any vents running out.
So we'll start with the layout of the cabinet.
Let's grab those measurements.
Kyle: Sounds great.
Nathan: It comes with these instructions, and it gives us the dimensions that we need to make our recess cavity.
So let's get started by finding the center between these lights.
28 1/2 inches.
So 14 1/4" will be our center mark.
So now that we have that mark, we need to set our height.
We have a 36-inch mirror on the front of this, but the back's a little bit smaller.
If we go up 36 inches off of this paint line, it kind of puts it at a comfortable height in line with the top of the tile on your shower.
So if I bring over a level mark...
Right there.
Okay.
So that would be the top of your mirror.
Do you think that's good height?
Kyle: That looks great.
Nathan: All right.
So now that we have our center line and we have a height to work to, I'm gonna do the plumb line for the center of our cabinet.
All right.
So we have the top of the mirror.
And then we have the body, the back side of it, which is 3 inches down.
So that's the top of our cavity there.
And we know that we need to come down 30 1/4".
30 1/4.
So if I put my tape right on 30 1/4 -- a little trick.
I can actually use the hook of my tape to score a line there.
So this is the bottom of the cavity.
Then we know our mirror is gonna overhang another 3 inches.
So what's nice is we're gonna cover a lot of this unpainted wall.
Kyle: Great.
Nathan: Now we're ready to go left and right.
For that, we know that we need to go off of our center line 10 3/4".
Right there.
Kyle: Mm-hmm.
Nathan: Now we just really need to start connecting the dots.
We'll connect everything with the level, and that's gonna show us what we need to take away.
And then that one.
All right.
So now that we have the layout, we know we have a stud here and we have a stud here.
So we'll have to work around those.
What I'd like to do between these lights... ...is just cut out a little hole that I can reach in with my hand, check for a wire or check for a vent.
Kyle: Great.
Nathan: I feel pretty safe cutting a small hole.
What I like to use is an oscillating tool.
I have a special drywall blade here.
And you can see it's got these depth gauges.
So 1/4 inch, 1/2 inch, three-quarter.
We know we probably have half-inch drywall.
I'll cut right to that point.
It'll be a nice, controlled cut.
If we like it, we can cut the big hole.
Kyle: Great.
Nathan: And for safety, we cut the power off.
♪♪ ♪♪ All right.
So we've got some insulation behind it, which is pretty normal in bathrooms these days.
We can tell this was remodeled in the '90s or the early 2000s.
There's some insulation in there for some sound dampening, probably.
So we can move that out of the way.
Okay.
So you can kind of push this to the side.
You can reach up.
All right.
Nice.
I don't really feel anything there.
I feel a little blocking right here against this stud.
Kyle: Yep.
Nathan: We have our other stud right here.
Reaching up.
I don't feel any electrical.
So I think these electricians were really on the ball.
They probably ran their wire up, over, and down, knowing that you were gonna be screwing through here to put a medicine cabinet.
Or they might have gone all the way up to the top light, over, and down -- path of least resistance.
So I feel pretty safe.
I don't feel any vents.
I think we can open this up.
Kyle: That sounds great.
♪♪ Nathan: You have pretty good depth.
At least that three inches we're looking for.
What we'll have to do is we'll switch the blade and do a deep cut here and here, there and there.
We'll pull those studs off, and then we'll notch out the next ones.
♪♪ ♪♪ All right.
Now that we have everything opened up, we can see that this was kind of a new-construction side.
This here is original.
You have your lath and plaster nailed to your studs.
Probably not load-bearing considering some of the joinery, so we're definitely safe to cut this a little bit.
What I'd like to do is actually notch these out.
So we only need three inches from the face of the wall back.
So on this side here, there's 3 inches.
So I'm gonna take out probably 3 1/4 for safety.
So if I go 3 1/4 this side, we'll take out an inch.
And then this side over here, maybe about 3/4".
To do that, I'm just gonna make some relief cuts all the way up.
[ Saw buzzing ] Then I take a sharp chisel and my hammer and just real slow, real delicate, just chisel all those out, and we'll have the cavity we need to start framing things back together.
Kyle: Great.
That sounds awesome.
Nathan: So we did a relief cut on the bottom and on the top about 3/4".
And I picked up some 3/4-inch pine here.
I'm going to put in some construction adhesive, kind of bed it inside that.
We'll set that down in here, and that will kind of act like a liquid shim.
We'll do the same to the top.
[ Drill whirring ] We're gonna take those same 2x4s that we cut out earlier.
We're actually gonna inlay it on the right and on the left.
Then the framing is pretty much done.
Kyle: That's great.
Nathan: Right there is good.
All right.
♪♪ All right.
Let's put the glass shelves in now.
Last shelf?
Kyle: That's the last one.
Nathan: It looks pretty good.
Okay.
A little bit of homework, though.
Some joint compound at the top.
Stand it.
Little bit of paint all around.
It'll blend right in.
Kyle: Great.
Nathan: Let's see how it looks closed.
Kyle: Absolutely.
Nathan: Nice, strong magnet.
Kyle: It looks great.
Nathan: Very cool.
Enjoy it.
Kyle: Thank you so much.
Nathan: You're welcome.
Kyle: Have a good day.
Nathan: You too.
♪♪ Mark: Today I'm headed to see a homeowner that wrote in about an indoor charcoal grill.
He had a general inspection on the chimney, and the inspector asked him not to use the chimney until he had a mason look at it.
I know these diagnoses can be tricky.
There's a flue involved.
There's a fireplace involved.
So what I've done is I've actually sent a crew to set up scaffolding before I arrive.
Kenny: Hey, Mark.
Mark: Kenny!
Kenny: Hey.
Good to see you.
Mark: How are you?
Kenny: Not so bad.
Mark: All right.
Oh, I love this place.
It's vintage.
Kenny: Thank you.
We love it, too.
It's from the 1960s.
I sent you an e-mail about some work in the kitchen.
Mark: Yeah.
That was a great e-mail, by the way.
I can't wait to see this piece.
Kenny: So let me show you.
In here, we've got a kind of special piece -- the indoor charcoal grill.
Mark: Oh, this is great.
Kenny: I really liked it.
There's a lot of history to it.
In fact, you can see down here, the original builders left an autograph.
Mark: I love that.
Kenny: "1962.
Bill and Bob."
Mark: So you got an autograph from Bill and Bob.
That is priceless to me.
I love that.
Kenny: That's great.
I really want to get it functioning.
The inspector was telling me that it's not in a working state, but I wanted to get your opinion on that.
Mark: Okay.
First thing I see is this little knob.
That represents a rotary damper.
There are two kinds of dampers, this rotary and a poker, which is just a handle in the middle of that door that pokes up.
But if I twist that a little bit -- you can hear me moving it.
[ Metal rattles ] Kenny: I see.
Yeah.
Mark: Okay.
Oh, you know what?
Okay.
If you put your hand up there... Kenny: Okay.
Mark: You feel how rough that wall is?
Kenny: I can feel that.
Mark: Yeah.
That's probably what the inspector is talking about.
The only problem I have with that is it may impede the smoke.
And that's probably what he's talking about.
I do like the wall.
It's structurally sound.
The mortar is tight, so that's good.
But I think we should light a fire in here just to make sure that the flow of the smoke does go up the way we like it to.
Kenny: All right.
Sounds good.
Mark: All right.
Let's get going on that.
♪♪ All right, Kenny.
This is the moment of truth.
Kenny: All right.
Let's see how it goes.
Mark: I'm gonna take this bag, do a little flame...
Okay.
I like it right off the bat.
You see the way that flame is being pulled up?
Kenny: There's no smoke coming in the house.
Mark: Okay.
Look at the smoke.
Look at how it's being pulled up as well.
Those are the two things that I love right off the bat.
Kenny: That's getting pretty strong.
Mark: It's getting very strong, which is another good sign.
So you can see how consistent that color is.
Usually there's a blue, there's a lighter orange, there's more of a yellow.
Sometimes there are gases and other products in what we burn.
But again, this one was consistent.
And again, you can see that smoke being pulled all the way through.
Kenny: So that's a good sign.
Mark: That's a great sign.
But, Kenny, I do see a problem.
You see all this streaking water right here?
Kenny: This back here.
Mark: Yep.
And you can see this white hue?
Kenny: I do.
Yeah.
Mark: Okay.
That's what we call efflorescence.
And it's actually a chemical reaction between the materials that are right here.
And that means there's some kind of leak.
Kenny: Okay.
Mark: So we should probably run outside, get on that roof, and see if there's any damage.
Kenny: Okay.
Sounds great.
Mark: Looks like the bag has burnt itself out, so that's good.
Let's take a look at the roof.
♪♪ All right, Kenny.
Let's see if we can find the kitchen flue.
Kenny: All right.
Mark: [ Sniffs ] Nothing here.
Oh, smell that one.
Kenny: Yeah.
I smell some smoke.
Mark: It smells like the burn we just did, right?
And this one has heat coming out of it.
So that's the burner.
One of the things I don't like is you can see these flues are all at the same height.
Kenny: Okay.
Why is that a problem?
Mark: There's a couple things.
It can induce downdraft, which is not good.
And it can also transfer smoke from flue to flue.
So that's why we stagger them.
But there are a couple of things that I do see that are good.
Again you can see this brick is intact.
Unfortunately what I do see as well is this moss.
Kenny: Yeah.
Under the lip here, hiding.
I see that now.
Mark: Yeah.
So that indicates water infiltration.
So if we look up top on this concrete crown, you can see these cracks.
Kenny: Yeah.
Mark: And the cracks are pretty much throughout.
This is a big crack right here that actually goes all the way around the chimney.
That's not a good thing because Mother Nature will push that water right through.
And I think that's a lot of our problem.
And if you look over here, we have a hump.
Kenny: Yeah.
Look at that.
Mark: Yeah.
So the problem with this hump is it redirects water maybe into places we don't want it to go into the kitchen.
Kenny: Right into the kitchen.
Mark: Yeah.
Exactly.
But I think if we stagger these flues, we change out this concrete cap, you're gonna be in great shape.
Kenny: Okay.
Cool.
Mark: So let's get going.
Kenny: Yeah.
Let's get to work.
Mark: Okay.
♪♪ All right, Kenny.
Let's grab those screens.
I'll grab these.
Now that we have our safety gear on, let's get at it.
♪♪ ♪♪ ♪♪ All right.
So, masons would always leave keepsakes anytime they did a concrete cap or a chimney, and they would be strategic about it.
Look at this.
We got an old pack of cigarettes.
I got a soda can right here... and another soda can right there.
♪♪ Now we're going to extend two of the flues.
♪♪ Kenny: How's that?
Mark: That's good.
♪♪ All right, Kenny.
Now it's time for the concrete cap.
So the first thing we're gonna do is we got to close up this cavity.
So what we're gonna do is take some re-rod.
Kenny: I'll grab one too.
Mark: Yep.
Grab one for me.
And we're gonna go the length of the chimney.
Just like that.
Kenny: Just like this.
Mark: Excellent.
Now you have the short pieces of re-rod.
Kenny: Yeah I got some cut up down here.
Mark: All right.
Great.
Nice job.
We're just gonna go like this.
Kenny: Put them across?
Mark: Put them across.
Kenny: I'll get one at the end.
Mark: And one at the end.
So, Kenny, this piece of wire, if you can check it out, has two eyes to it.
All right.
We're just gonna take those eyes... and we're gonna take our wire twist right here.
One eye, two eye, and all we do is twist.
All right, Kenny.
So we're gonna take this wire mesh.
We're gonna put it over the flues.
It's gonna sit on top of the re-rod.
Now, as you can see, I already pre-cut the mesh.
Kenny: It fits like a glove.
Mark: Fits like a glove.
And you can see that that's gonna stop the concrete from falling into the cavity.
Kenny: Okay.
Mark: All right.
So right now we're ready for concrete.
Kenny: All right.
Let's do it.
♪♪ Just the base layer?
Mark: It's the base layer.
It's a good consistency.
It'll be easy for us to spread.
♪♪ Now, just remember we're gonna do half the thickness right now, and then we're gonna drop some more reinforcement in.
♪♪ ♪♪ You can see how that edge is already starting to stiffen up.
Kenny: Yeah.
Mark: Why don't you bring the number 9 wire in?
Again, pre-cut.
Kenny: You said this is for reinforcing.
Mark: We're gonna dip this into the cap.
Oh, yeah.
This is beautiful.
So you're just gonna take your trowel and tap this into the mix.
So this wire is gonna be right in the middle of our pour.
Kenny: Okay.
Give it a lot of strength?
Mark: That's right.
Kenny: Okay.
Mark: Again, this is another step that most people skip.
And again, you're not gonna worry about that divot 'cause we have more concrete coming on top of it.
♪♪ ♪♪ ♪♪ All right.
So let's put these screens back on.
This will keep the animals out.
I do have something picked out for this flue here, Kenny.
Because you're gonna be cooking out of this flu, I want to put this metal cap on there.
That'll keep those water streaks away.
Kenny: That looks beautiful.
Mark: It's most economical just to use one.
We could put one on the entire cap That would be very expensive.
I mean in the thousands.
Kenny: Sure.
So we'll address the problem area and just use one cap.
And if you ask me, I think that looks great.
Kenny: That looks fantastic.
Let me finish this one off.
You just put that one on with a couple screws?
Mark: That's it.
All right, Kenny.
Looks like we got all the moss.
Kenny: Yeah.
It looks great.
But there's just one more thing I want to do if you're okay with it.
Mark: Okay.
Kenny: I got pen here.
Let's sign the chimney.
Mark: I see what you're doing.
I love it.
I love it.
Oh, yeah.
"Kenny and..." "...Mark."
Kenny: Beautiful.
Mark: Just like downstairs.
Bill and Bob.
Kenny and Mark.
I love it.
Kenny: I love it, too.
Well, thank you so much.
Mark: All right.
You got it, Kenny.
Kenny: That's a lot of fun.
Mark: Yeah.
I had fun, too.
Thanks.
Kenny: My pleasure.
♪♪ ♪♪ Kevin: Mark, what is going on here?
Have you been dumpster diving?
Mark: Well, something like that, Kevin.
Every time I dig, I keep my fingers crossed and I hope to find something.
Kevin: Is this all your stuff?
Mark: This is all my stuff.
Kevin: You found all this?
Mark: Yeah.
Kevin: I guess it makes sense.
You're our digger.
I didn't even think about that.
But foundations and footings.
That's all on you.
Mark: Sure.
Kevin: No kidding.
Mark: Yeah.
So this, I'm surmising, came from a kitchen.
I was digging a footing one day.
I hit this kettle first and then started to be really careful because I knew other stuff was around.
Kevin: So pots, a couple different pans, a little tea kettle, a teapot?
Mark: That looks like a little teapot right there.
Yeah.
It's in pretty good shape.
Kevin: And this one?
Mark: This one caught my eye because I know what it is.
It's a leg for a Ben Franklin stove.
I'm a Ben Franklin guy, so couldn't resist.
Kevin: Right up your alley.
Mark: Yeah.
Kevin: That's some beefy steel right there.
Mark: Yeah.
Kevin: So was it, like, a garbage pit, you think, where they just kind of tossed stuff out back?
Kevin: Something that people might not know is back in the day -- I'm talking early 1900s, late 1800s -- people used to burn their trash literally right in their backyard.
So I'm surmising that this group came from a burn.
Kevin: Look at you.
Mark: Form work that I had to demo.
These nails have come out of houses.
Those are late 1800s.
Kevin: Square-cut nails.
Right.
Mark: Yeah.
Again, on a dig, I found these two guys.
Kevin: Yeah.
You know, there's a spot across the street from where I grew up at my best buddy's house where there's a hundred Matchbox cars, 'cause we used to play with them back there, and they'd all get lost.
Mark: Maybe that's how I found those.
Kevin: That is very cool.
You or your... Mark: No.
These are my contemporaries.
Right.
This is used to finish a block wall or a brick wall.
And they used to dive a can of beer right into the core of the block.
Kevin: Is that right?
Just a tradition?
Mark: Yeah.
Doing some demo.
Tradition.
Kevin: King-size Knickerbocker.
Boy, they used a lot of steel in those things back in the day.
Mark: Tradition has ended, by the way, Kevin: Okay.
Mr. Thomas da Silva... Mark: Yes.
Kevin: ...1949, Watertown, Mass.
And is there -- Oh, there's a note inside.
Mark: There is.
Kevin: Did you read it?
Mark: I had to.
I couldn't resist.
Kevin: And?
Mark: Love letter.
Kevin: Oh.
A good one or a bad one?
Mark: Good one.
"Where are you?
I miss you."
Kevin: That's very good.
And what year and what paper is that?
Mark: I was putting in a fireplace in an existing house.
So I had to do some demo.
Behind the wall, I found this.
Boston Globe.
And if you flip back, you'll see the date -- 1925.
Kevin: Oh, very, very cool.
And then, of course, we find these all the time.
Mark: Yeah, yeah, yeah.
Kevin: Either 'cause they've been emptied by the worker or, like you say, thrown away.
They go through this stuff.
Mark: Yeah.
But this is the whole show.
I mean, these are medicine bottles.
This is a wine bottle That's a milk bottle, of course.
And that is the gem Kevin: I have to tell my dad we just found his aftershave.
Mark: Yeah.
Old Spice.
Kevin: What is that, clay or porcelain?
Mark: I think it's porcelain, but 1930... Kevin: That is so cool.
Mark: ...original.
Kevin: So you're just into it.
You find them and you say, "I'm gonna keep them."
Mark: Yeah.
You dig into the ground.
You find something like this.
I don't know what it is.
But I find a personal connection to everything.
So I brush things off -- again, hoping to find more.
It's like a treasure.
Kevin: Good for you.
Well, we appreciate you sharing your treasure.
Mark: All right.
Kevin: Very nice.
Mark: Thanks, Kevin.
Kevin: Check out this roadster.
Mark: Yeah, really.
That's the fast one.
Kevin: We used to blow these up with firecrackers.
Mark: Wow.
[ Laughs ] Kevin: [ Imitates explosion ] Kevin: Next time on "Ask This Old House" -- Jenn helps a homeowner who is struggling to manage her gutter runoff.
Jenn: See all the water coming out of this downspout?
This is gonna have a place to go.
Kevin: Then we meet a carpenter who found his calling teaching the next generation.
And Heath replaces a ceiling fan that lacks the proper support.
Heath: It's all designed to hold the weight and the vibration of a fan.
Kevin: All that on "Ask This Old House."
Funding for THIS OLD HOUSE is provided by The Home Depot and Renewal By Andersen.