Norm Knowledge
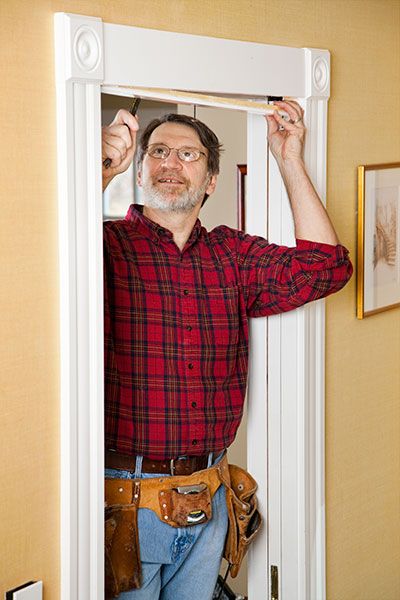
It doesn’t take a diehard TOH fan to figure out that master carpenter Norm Abram has learned a thing or two over the years. Just flip to the back of the magazine (or on your tablet!) each month to get his pro answers for readers’ tough DIY questions. Here, we’ve gathered the latest set of his tips to help you in a how-to pinch. Learn how to recess screwheads, squeeze a fixed shelf in a closet, and even prevent shoe-molding from splitting when hand-nailing.
Mitered Joints for Narrow Window Casing
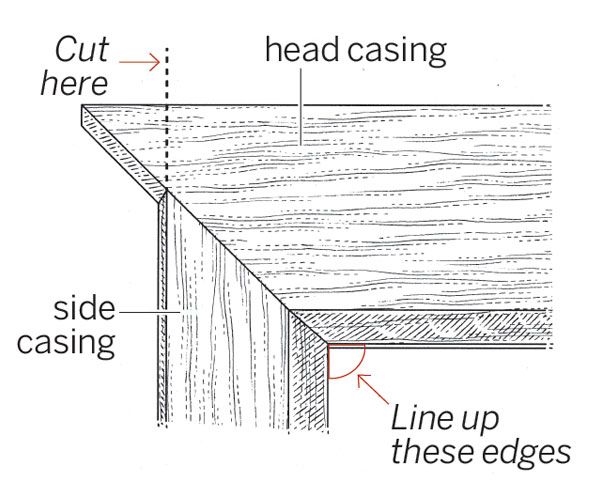
Q: The side trim on some of my windows has to be narrower than the head casing. How do I make mitered joints?
—Anthony Tangi, Philadelphia
A: I’ve encountered this situation when a window or door is too close to a cabinet or a wall for full-width side casing to fit. Here’s what to do. Cut 45-degree miters at the ends of the head casing and at one end of each side casing, then rip down the sidepieces to the width you want. Now place the miters together and line up the inside edges, as shown. Mark where the outside edge of each sidepiece meets the head casing. Trim the ends of the head casing at those marks with a square, 90-degree cut. The small portion of end grain that’s exposed when the casing is assembled will be hidden by the wall or cabinet that you’re up against. If the backs of the sidepieces aren’t flat, you may have to shim their outside edges to make them flush with the head casing.
Make Face-Grain Wood Plugs: Step 1
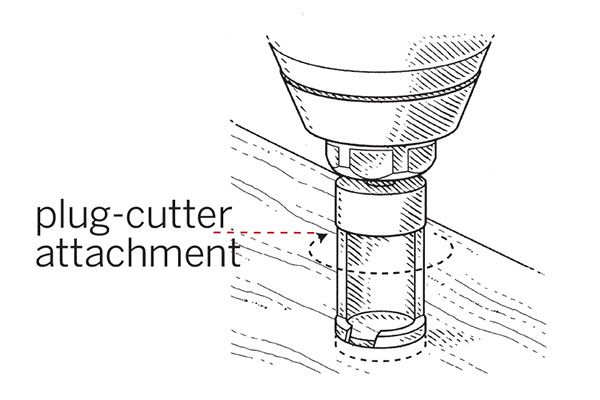
Q: I can’t find face-grain wood plugs to match the wood I’m using on a stair project. What now?
—Todd Lockwood, Marysville, Wash.
A: Why not make your own? You need a drill, a scrap of the same wood you’re trying to match, and a plug cutter. These cutters carve plugs from ¼ inch to 1½ inches in diameter, as well as metric sizes, to match the diameter of the counterbore, the cylindrical recess in which the screw sits. Make sure your cutter can be used with a drill—some require a drill press—then follow these steps.
Clamp the scrap to a workbench and put the bit in the drill. Hold it perpendicular to the wood’s face, turn it on, then slowly sink the cutter about ½ inch into the scrap. With the bit spinning, lift it straight out. Repeat in different places on the scrap so that you’ll have a selection of colors and grain patterns to match the wood being plugged.
Make Face-Grain Wood Plugs: Step 2
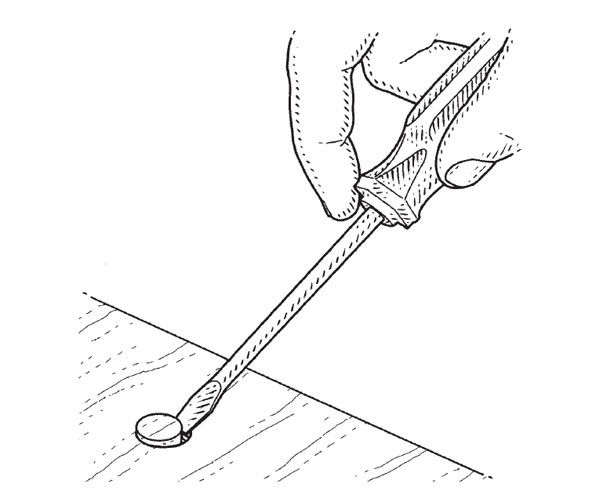
Snap the plug free. After the cutter has done its job, the bottom of the plug is still attached to the scrap. Insert a flathead screwdriver into the slot next to the plug and gently pry up. It doesn’t take much force to crack it loose.
Recess a Screwhead: Step 1
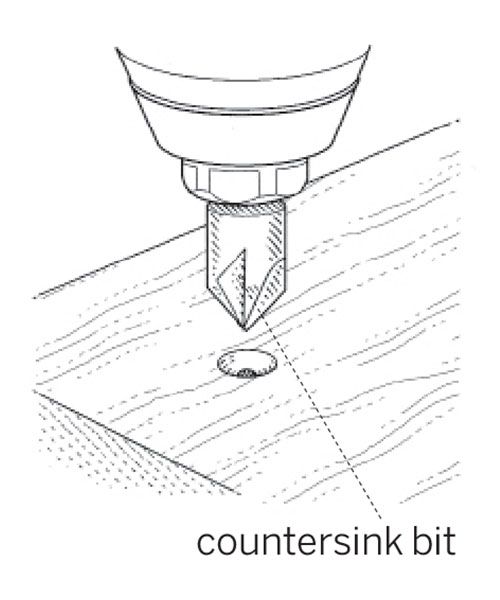
Q: I have some wood shelf brackets held in place with recessed screws. I’d like to add more screws for increased support, but how do I recess the heads?
—Eileen Lerch, Tullahoma, Tenn.
A: To recess any screwhead, you make a cone-shaped recess called a countersink. The traditional way to do this is with a dedicated bit, which allows you to make countersinks of different diameters. Here’s how.
Drill a pilot hole for the screw. Then, with the countersink bit centered in the hole and perpendicular to the surface, run the drill at high speed without applying much pressure. That’s how you get a clean countersink with no tear-out.
Recess a Screwhead: Step 2
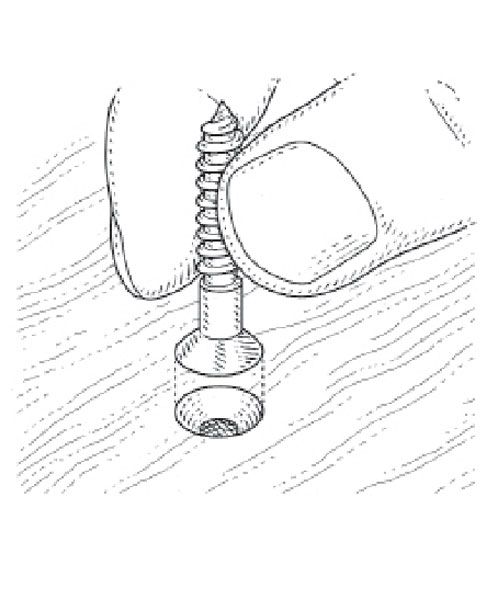
To get the screwhead perfectly flush, drill shallower than needed and place the screwhead over the hole to see how much farther you need to go. Drill a little deeper and check again. By sneaking up on the correct depth, there’s less risk of going too deep.
Cut Baseboards for Contours: Step 1
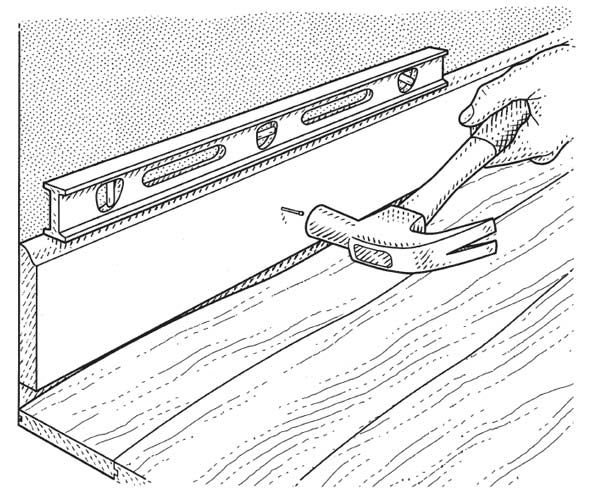
Q: I’m installing new baseboards, but in some places they don’t touch the uneven floor. Is there some kind of filler I can use to hide the gaps?
—Bob Tellez, Los Angeles
A: This is not a job for fillers, which are messy to apply, difficult to disguise, and not very durable. The better solution is to cut the bottom edges of the baseboards so that they follow the contours of the floor, a process called scribing. Some carpenters scribe with a compass, but my father just used a pencil and a scrap of wood. That’s the way I often do it, too. Here are the steps to a perfect fit.
Find the high spot of the floor. Rest the baseboard in position on that spot, level it, and tack it in place. Leave the nailhead proud so that it will be easy to remove later. Measure the largest gap between the floor and the bottom edge of the baseboard, then find a piece of scrap wood close to the same thickness as that gap.
Cut Baseboards for Contours: Step 2
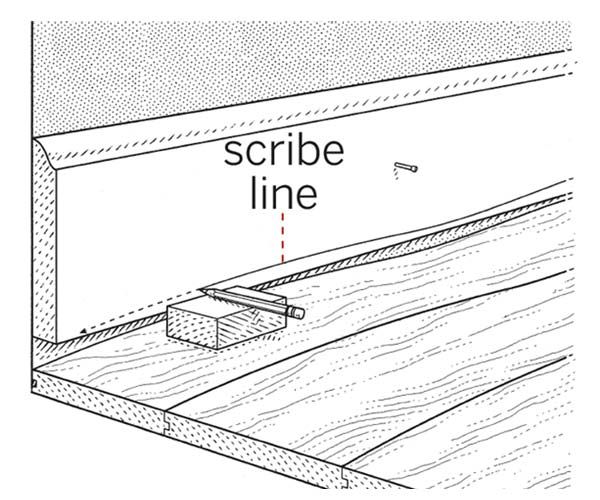
Holding a pencil tight against the scrap, run it along the floor and mark the baseboard, as shown. Now remove the baseboard and cut along the scribe line with a jigsaw or a trim saw. With either tool, angle the blade about 5 degrees into the baseboard’s back side. This makes it easier to fine-tune the scribe with a block plane. When the baseboard fits neatly against the floor, nail it in place.
Build, Install Interior Wall: Step 1
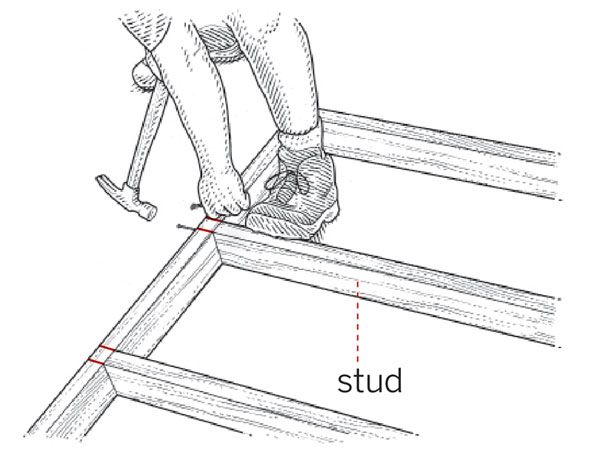
Q: I need to install an interior wall in a finished basement. Can I build it first and then tip it up?
—Paul DeLaricheliere, Henderson, Nev.
A: That’s the way I’d do it. But there’s a problem: When a wall is built to fit precisely in a space and you tip it straight up, the top plate will collide with the ceiling before the studs come into plumb. You could make the wall a little short and then shim it into place, but here’s a trick that averts all that fuss.
Frame the wall. Mark the floor and ceiling where you want the wall to land. Measure the ceiling height, subtract 3 inches (the combined thickness of the top and bottom plates), and cut the studs to that length. Cut the plates to length, lay them face-to-face on the floor, and mark both edges every 16 inches. Situate the studs between the plates at your marks, then drive two 16d nails through the plates and into the ends of the studs.
Build, Install Interior Wall: Step 2
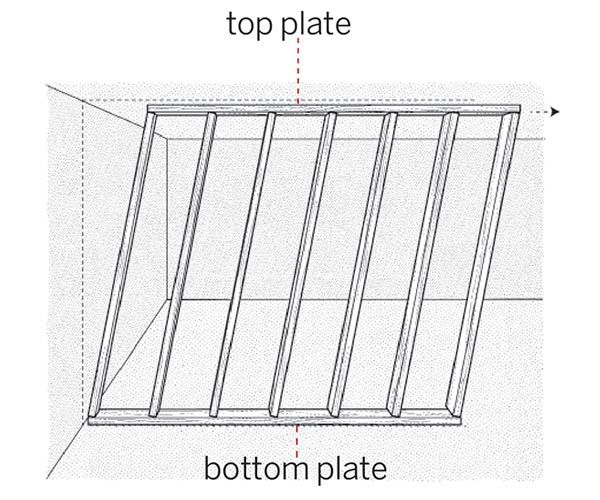
Tilt and rack. Set the wall’s bottom plate next to the mark on the floor and tilt the wall up. As it nears the ceiling, rack the wall slightly, away from the adjacent wall. This turns it into a parallelogram, reducing its height enough to give you the clearance you need. Once the plates are on their marks, push the studs plumb. The wall will snug up to the ceiling just right, ready for you to fasten the plates to the floor and the ceiling joists.
Fit a Fixed Shelf: Step 1
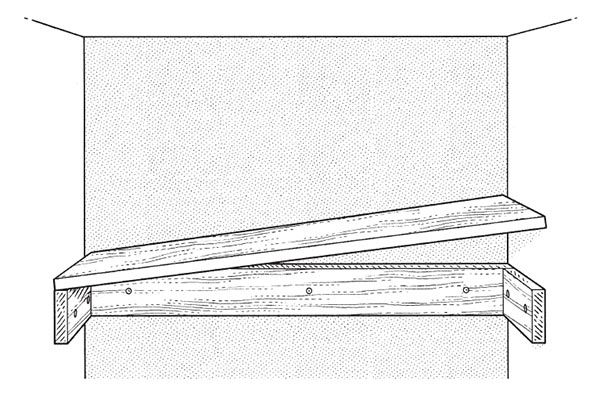
Q: I want to install a fixed shelf in a closet, but the walls have no square corners. How do I even begin?
—Denis Fuchs, Poulsbo, Wash.
A: Closet walls are seldom square, due to the buildup of joint compound in the corners. As a teenager working for my father, I installed plenty of 1×12 pine closet shelves and got pretty good at fitting them into irregular spaces. Here’s how I did it, all those years ago.
Cut the shelf. Measure the distance between the walls, add ¼ inch, and cut the shelf to that length, square on both ends. Now set one end on the cleat and the other against the wall, with the back edge against the back wall.
Fit a Fixed Shelf: Step 2
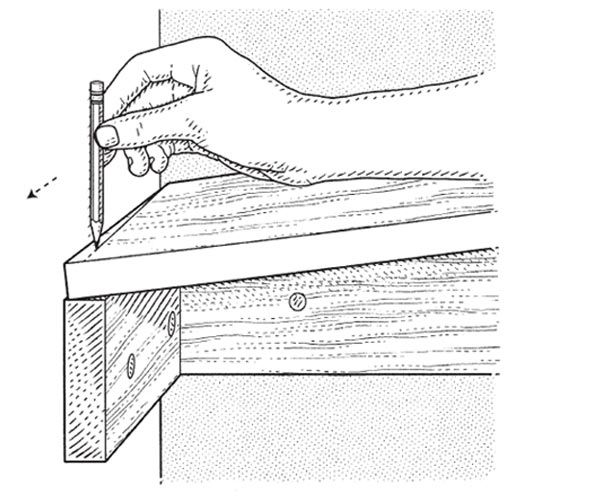
Scribe-fit the ends. Hold a pencil against the back corner with its lead
on the shelf end that’s resting on the cleat. Pull it toward you along the wall, as shown, marking the shelf as you go. Cut along this scribe line with a jigsaw, then angle the shelf the opposite way and repeat the process at the other end for a nice snug fit.
Prevent Shoe Molding Splits
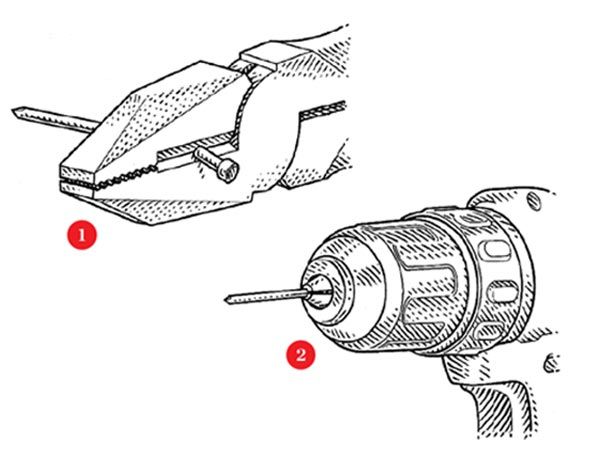
Q: No matter how carefully I hand-nail shoe molding, it often splits. Can I do anything to prevent this?
—Jason Stutts, Prosperity, S.C.
A: It’s always a good idea to drill a pilot hole before nailing trim with a hammer, especially if the wood is thin or the nail is close to the edge. But with this trick my father taught me, you won’t need to go hunting for the right-size bit. Just use one of the nails. First, cut off the nailhead so that the drill’s jaws can get a tight grip on the shaft (1). Then stick the cut end into the chuck, snug up the jaws (2), and drill away with the nail’s factory-cut point. You’ll get a perfectly sized pilot hole every time.
Fold a Sheet of Sandpaper
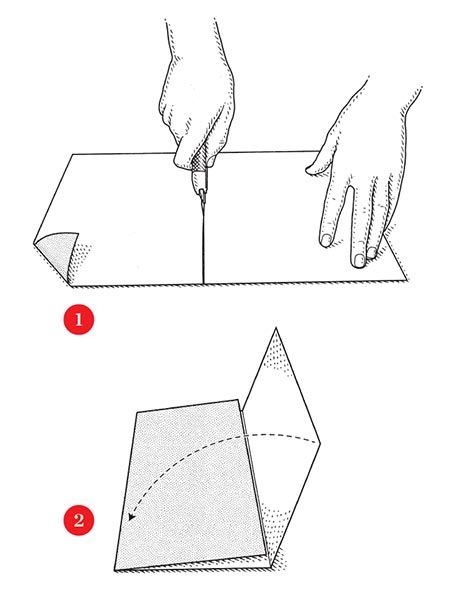
Q: What’s the best way to fold a sheet of sandpaper?
—Elaine Malkin, Oceanside, N.Y.
A: I didn’t used to give much thought to how I folded sandpaper. But then I realized that if the abrasive sides rubbed against each other, the grit would be worn even before it touched wood. That’s why I now cut the sheet in half across its width—rough-side down, to avoid dulling the knife (1)—and fold each half in thirds (2) so that only the smooth paper backing touches the abrasive. This keeps the abrasive sharp and makes the sandpaper easier to hold and far less bulky than a full sheet folded into sixths.
Install Front-Door Casing
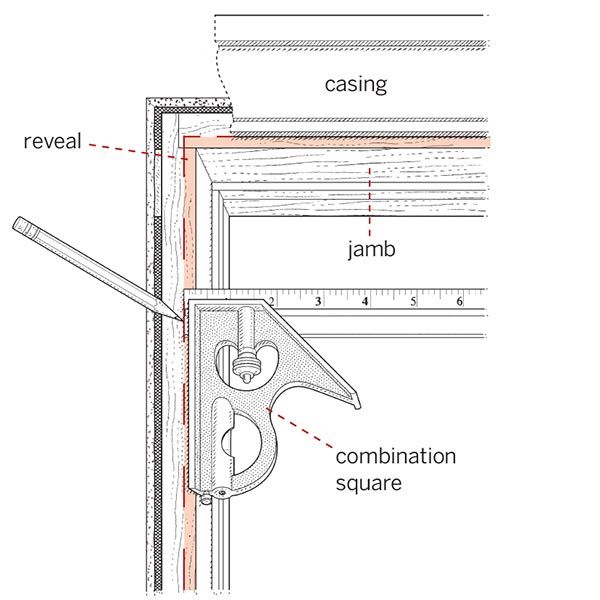
Q: My wife and I managed to square up the front-door frame that the builder botched. Now, what’s the best way to install the casing?
—Chris Costanza, Cincinnati
A: The trick to installing casing is to always offset the trim’s inner edge slightly from the jamb’s inside face. This creates a small step, called a reveal, that adds visual interest and prevents the unsightly paint cracks that occur when a casing is flush with that face. To make a consistent reveal, set a combination square to ¼ inch and mark the jamb edges, as shown. Then just line up each piece of casing with the marks and nail it to the edge of the jamb and to the rough framing under the drywall.
Drill Perpendicular Holes
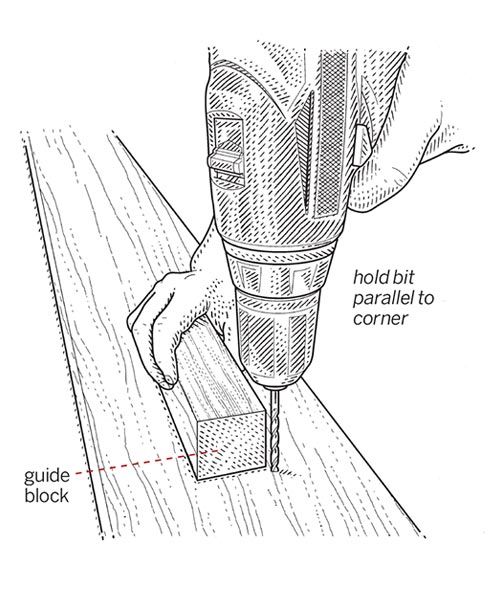
Q: What’s your secret for drilling perpendicular holes?
—Cathy Graves, Waxahachie, Texas
A: Here’s a trick I use when I don’t have a drill press or a jig: Place the drill
bit where the hole will be, then take a scrap block with a crisp 90° end and place its corner close to the bit, as shown. Now align the bit with the corner; it will be perpendicular to the surface you’re drilling. Remove the guide block once the hole is started, and concentrate on holding the bit at the same angle until you’re done.
Make Accurate Miter Cuts
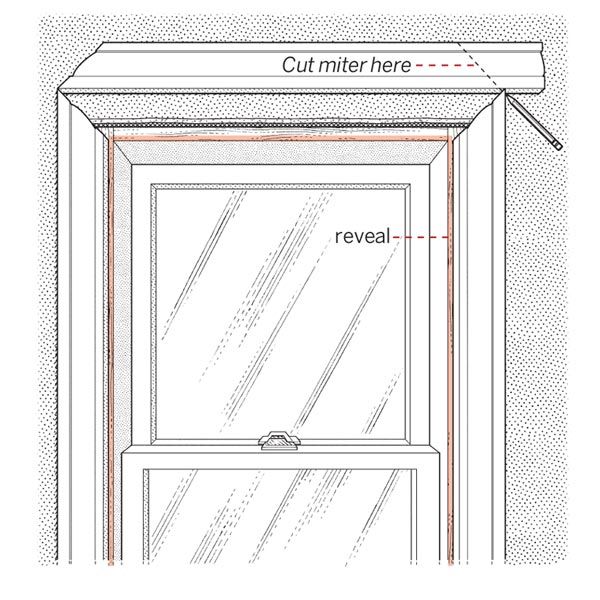
Q: When I’m installing window trim, my miter cuts are always just a little off. What am I doing wrong?
—Dan Droeg, Chandler, Ariz.
A: Assuming that your saw is cutting accurate miters, try putting away your tape measure and marking your cuts at the window. Start with the side casings: Hold them against the vertical reveal marks, mark and cut each piece where its inside edge crosses the reveal for the head casing, and nail them both to the window frame. Now miter one end of the head casing and hold it upside down on top of the side casings. Simply mark the second miter, as shown, and make the cut. If the window is square, and the wall flat, the head casing should fit perfectly every time.
Even Out a Basement Concrete Floor
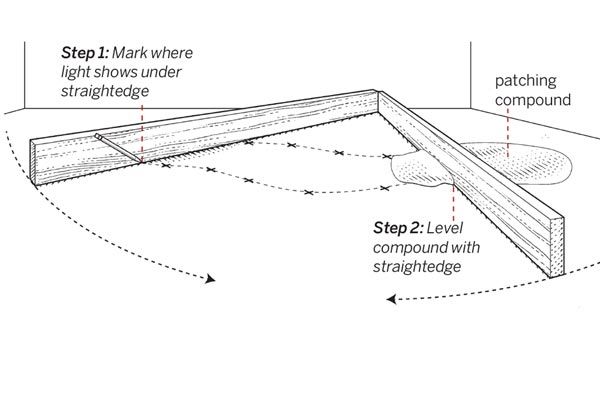
Q: How do I fix the uneven concrete floor in my basement before putting down engineered flooring?
—Christian Benyei, Bethel, Conn.
A: To find and get rid of the dips in your floor, you need a straight board at least 8 feet long and a pencil. Set the board on edge and move it across the floor, marking on either side of any low spot where daylight shows underneath. The marks will trace the outline of the dip, which you can fill with concrete patching compound and level using the board.
Toenail Studs to a Bottom Plate: Step 1
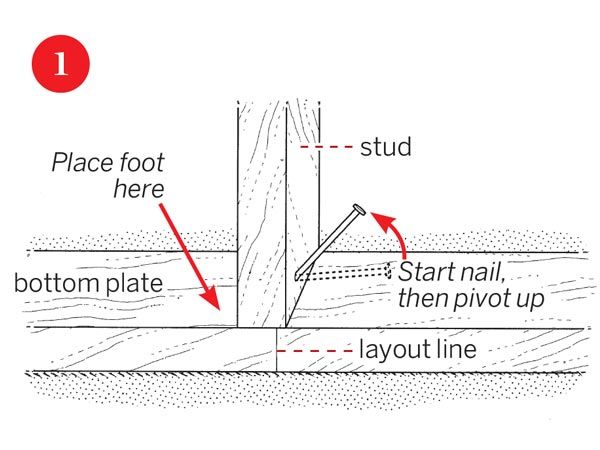
Q: Is there an efficient way to toenail studs to the bottom plate?
—Jeff Drummond, Birmingham, Ala.
A: Knowing how to toenail with a hammer is a useful skill. Here’s the method I use when framing—wearing work boots, of course.
Knock the stud ⅛ inch off the layout line on the plate. Brace the stud with your foot and tap a nail about ¼ inch deep straight into the stud’s face. Now pull the nail up to about 30° from that face.
Toenail Studs to a Bottom Plate: Step 2
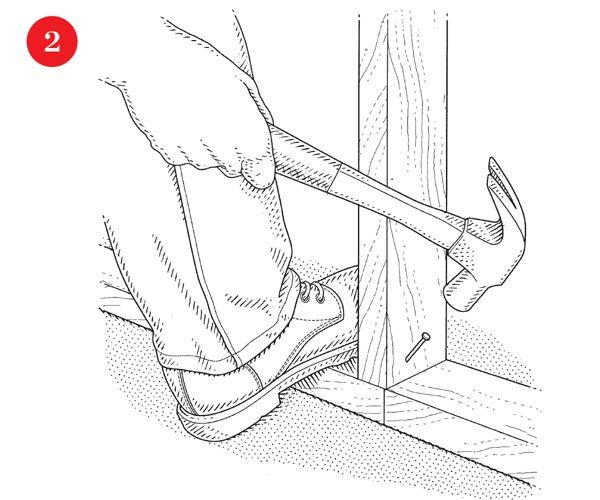
Keeping your foot in place, drive the nail into the plate. Your blows will nudge the stud back to its layout line. To prevent twisting, drive a second toenail through the same face, also using your foot as a backstop, then toenail through the center of the stud’s other face.
Determine if a Framing Square is Square
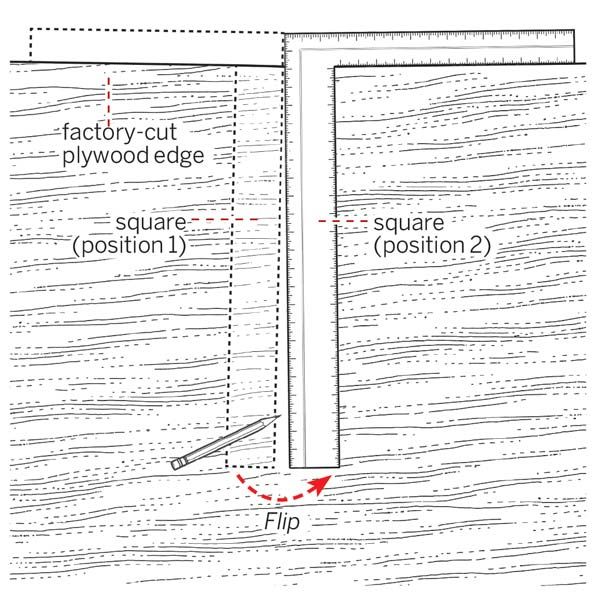
Q: How can I tell if my framing square is square?
—Jim White, Bakersfield, Calif.
A: That’s easy. Simply rest the square’s short leg (called the tongue) on the factory-cut edge of a plywood panel, and mark a line along the long leg (called the blade). Now flip the square over, hook the tongue on the same edge, on the point where the line meets the edge, as shown, and mark another line along the blade from that point. If the lines diverge, replace the square. New or old, it’s good to check a framing square frequently because it can easily spring out of square if dropped or banged against something.
Line up Deck Joists: Step 1
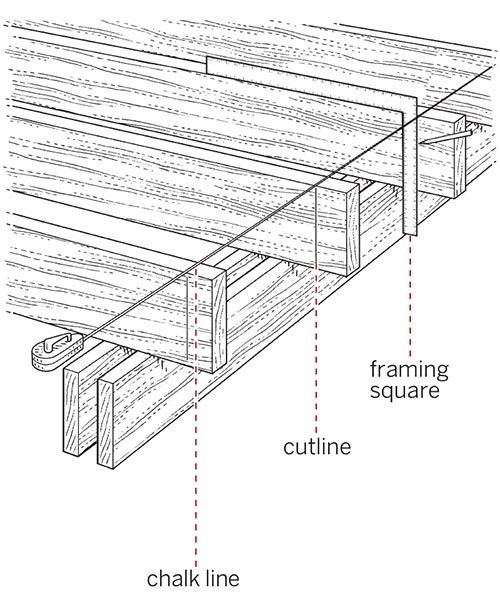
Q: I just started building my first deck. It looks pretty good so far, except that the ends of the joists don’t line up. I measured everything so carefully. What happened?
—Kevin Betker, Portland, Ore.
A: I’ll bet you committed a mistake that many people make: cutting the ends of the joists to a set length. But that only works on ledgers that are perfectly straight, and they seldom are. To correct this, go back and trim your joists using the following technique. It ensures that the band joist covering the ends of the joists will be arrow-straight as well.
Snap a line. Measure out from the house along the first and last joists to the length you want, then mark each one’s top edge. Stretch a chalk line between those marks and snap it, leaving a mark on the top edge of each joist. Now take a framing square, rest its long blade on the joist, and line up its short tongue with the chalk mark, as shown. Draw a vertical line along the tongue from each mark down the face of each joist.
Line up Deck Joists: Step 2
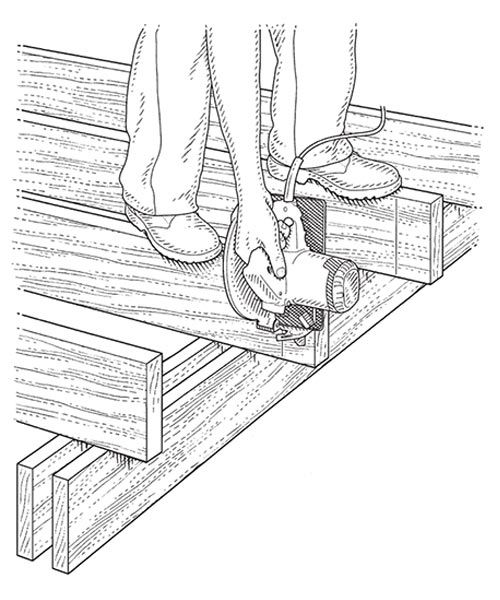
Trim the ends. Using a circular saw, slice through each joist along the vertical cutline. Note: If you work from above, as shown, gravity will provide an assist as you make each cut. When the band joist is fastened to the ends of these joists, it will be absolutely straight.