By Matthew Bauer and Zach Pritchard June 17, 2024
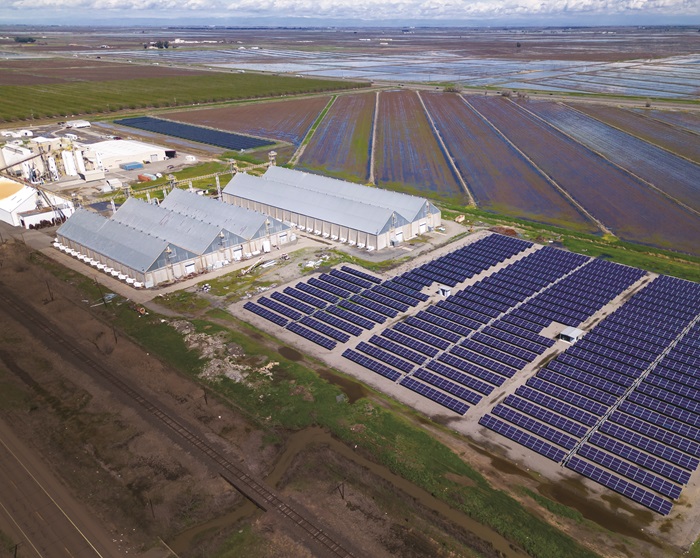
Solar panels provide energy at a California agricultural business. (Credit: Aziz Shamuratov)
From the cement and steel that make our buildings sturdy to the food products that sustain us, the U.S. manufacturing sector produces the building blocks of our modern society. But these products come at a price. Manufacturing accounts for a quarter of all energy-related carbon dioxide (CO2) emissions in the United States.
Driving down these emissions is a top priority at the U.S. Department of Energy (DOE), where we’re seeking out and investing in innovative solutions to decarbonize the largest source of industrial emissions: heat generation.
Heat is essential and pervasive in manufacturing, accounting for almost half of the sector’s CO2 emissions. Industrial heat is also diverse. Heat demand varies across industries, from the relatively low temperatures needed to pasteurize foods or remove moisture in papermaking to the high temperatures needed to produce cement or extract metals from ore.
Today, about 95% of all industrial heat is generated by burning fossil fuels, but making the products we can’t live without shouldn’t require us to make pollution that we can’t live with. That’s why, in 2022, DOE created the Industrial Heat Shot to transform the way that manufacturers generate and use heat.1
The Industrial Heat Shot is part of DOE’s Energy Earthshots Initiative, a series of commitments to achieve the major technology breakthroughs needed to solve the climate crisis. The Industrial Heat Shot aims to develop cost-competitive industrial-heat-decarbonization technologies with at least 85% lower greenhouse gas (GHG) emissions by 2035.
The Industrial Heat Shot supports the overarching strategy detailed in DOE’s Industrial Decarbonization Roadmap, which presents a staged research, development and demonstration approach to dramatically reduce emissions, increase United States manufacturing competitiveness and create high-quality jobs.2
Given the diversity of industrial heating demand, there can be no one-size-fits-all solution to providing clean heat. To tackle this challenge, we need a full portfolio of solutions — and solar energy has a clear role to play, whether by providing clean, renewable electricity or by harnessing the heat of the sun directly.
One approach for decarbonizing industrial heat is to take a lesson from the transportation and buildings sectors: Electrify as much as possible. Electrification solutions for industry range from simple resistive heating to industrial-scale heat pumps that put waste heat to good use and advanced electrotechnologies that deliver energy directly into process materials.
On top of reducing emissions, many of these electrified heating technologies have the potential to reduce energy use and even improve product quality.
In February 2024, DOE took a major step toward realizing this opportunity by launching Electrified Processes for Industry without Carbon (EPIXC).3 Over the next five years, EPIXC will work with a broad coalition of manufacturers, national labs, universities, labor unions, tribal nations and community partners to drive the electrification of industrial heat.
EPIXC will accomplish its goals through education and training to develop the industrial workforce of the future and through investments in research, development and demonstration projects that will move innovative electrification technologies toward commercialization.
Advancing these technologies is a critical piece of the puzzle, but clean, electrified industrial heat can only exist if facilities have access to clean energy. Facilities can generate clean energy onsite and lower their emissions with photovoltaic solar technologies, often in the form of rooftop solar panels.
When onsite generation is not available, there are other ways that companies can obtain clean energy, usually through a short- or long-term commitment to purchase electricity from utilities or competitive suppliers.4
While electrification can meet many of our industrial heat needs, it isn’t a silver bullet. We also need to develop technologies that can harness solar, geothermal and nuclear* heat for industrial use.
DOE has been funding low-cost, reliable concentrating solar-thermal (CST) technologies, which use mirrors to reflect and concentrate sunlight onto a receiver.
The energy from the concentrated sunlight then heats a high-temperature fluid in the receiver to efficiently convert solar radiation into thermal energy.
CST technologies have great potential to decarbonize the industrial sector because they can directly produce both the low-temperature heat needed for food processing and the high-temperature heat needed in the industrial sector.
DOE funds research to advance industrial uses for solar-thermal technologies, specifically in the cement, hydrogen and chemicals sectors.5
Of course, the sun doesn’t shine 24 hours a day. Just as we expect batteries to play a role in decarbonizing the electric grid, thermal batteries — or thermal energy storage — will play a role in decarbonizing industrial heat as critical components in future industrial energy systems.
DOE is supporting the deployment of onsite clean energy technologies like solar photovoltaics, solar thermal and thermal storage through the Onsite Energy Technical Assistance Partnerships, which provide regional technical assistance, market analysis and best practices for industrial facilities and other large energy users.
By generating and storing electricity and heat directly at their facilities, manufacturers can save money, reduce uncertainty associated with fuel prices, and gain greater control over the use of clean energy in their processes.6
The challenge ahead of us is immense, but so is the prize. Achieving the goal of the Industrial Heat Shot would put the U.S. industrial sector on course to reduce its annual GHG emissions by 575 million metric tons CO2-equivalent in 2050 — roughly equal to the emissions generated by all passenger cars on the road in 2020.
Renewable energy sources like solar will be critical to reaching this goal, but we’ve just scratched the surface. An even wider range of solutions like clean hydrogen, renewable fuels and alternative low-temperature processes will also have a role to play.
The future of U.S. manufacturing lies in these emerging processes and technologies that will be brought to our factory floors through public-private partnerships and bold innovation.
* To align with the perspective of stakeholders at the American Solar Energy Society, Solar Today does not encourage the use of nuclear fission as a power source.
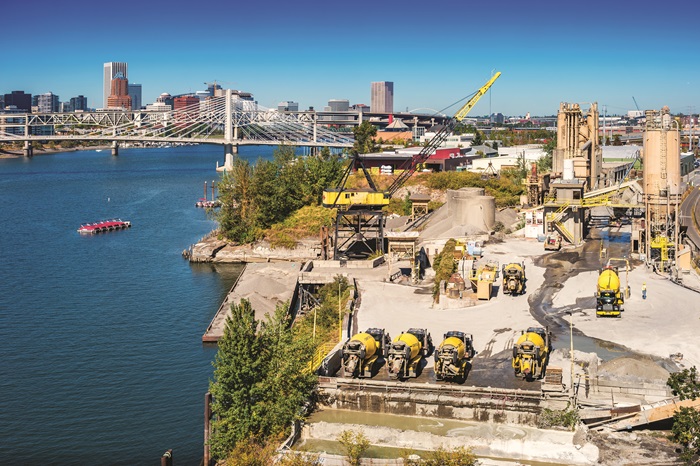
Sources
- https://tinyurl.com/Iheatshot
- https://tinyurl.com/DecarbRoadmap
- https://tinyurl.com/EPIXC
- https://tinyurl.com/BPIndustrial
- https://tinyurl.com/SolarIndustrial
- https://tinyurl.com/OnsiteTAPs
About the Authors
Matthew Bauer is the program manager for the U.S. Department of Energy Solar Energy Technologies Office Concentrating Solar-Thermal Power (CSP) team. Since 2015, he has worked with the CSP research and development community to identify promising CSP-relevant technologies and solve technical risks impeding such technologies from commercial adoption.
Zach Pritchard is a technology manager with the U.S. Department of Energy’s Industrial Efficiency and Decarbonization Office, where he supports research on and development and demonstration of technologies that can reduce emissions from industrial process heating.